Um detector de falhas ultrassônico é o equipamento projetado para detectar defeitos em um objeto sem danificar sua integridade. As deformações são detectadas através do impacto das ondas ultrassônicas no objeto. O equipamento está em grande demanda, pois o método de seu funcionamento é o único que permite fornecer os resultados diagnósticos mais precisos sem desmontar o objeto de pesquisa.
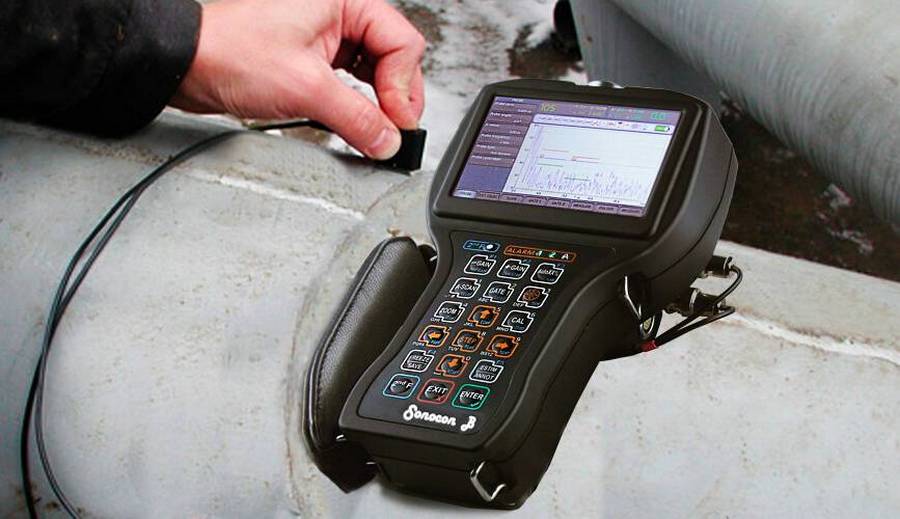
Detector de falhas ultrassônico: informações gerais
O ultrassom passa por uma camada de ferro sólido e é capaz de detectar a presença das menores rachaduras que possam estar dentro do objeto. O dispositivo será capaz de detectar um defeito a uma profundidade de 5 a 50 milímetros com alta precisão. O equipamento considerado pode ter diferentes níveis de sensibilidade. Este indicador depende do tamanho e dimensões do defeito detectado. O escopo do dispositivo é muito amplo, mas na maioria das vezes eles são usados para determinar a qualidade dos metais na produção.Os dispositivos têm operação intuitiva, proporcionam um uso unificado e eficiente e são caracterizados por maior precisão, o que permite obter resultados de alta qualidade e detectar e corrigir em tempo hábil várias falhas de produção.
Princípio do controle ultrassônico
O tipo de aparelho considerado geralmente é usado para controlar o nível de resistência nas soldas. Nesse caso, o dispositivo funciona da seguinte forma durante a operação: ondas acústicas específicas são direcionadas para as chapas metálicas, causando vibrações na caixa. Podem ser dos seguintes tipos:
- Hipersônico;
- ultra-sônico;
- Som padrão;
- Infrassônico.
Durante a passagem do ultrassom, o espaço pelo qual ele se propaga forma oscilações uniformes em relação ao seu ponto de repouso. Para sólidos, podem ocorrer vibrações transversais/longitudinais, o que permite controlar a qualidade das soldas com a máxima precisão. A velocidade de propagação e fornecimento das ondas descritas é diretamente dependente da força/ambiente interno do objeto em estudo. A intensidade das ondas pode ser ajustada. À medida que a onda se propaga, sua força gradualmente desaparece. Com base no controle da taxa dessa extinção, será possível julgar a resistência da costura. O aparelho, por outro lado, exibirá o coeficiente de atenuação do ultrassom, criando-o com base no grau de absorção e espalhamento. A precisão final é muito alta, então você pode obter ideias específicas sobre a qualidade do metal, a resistência da costura e a ausência/presença de outros defeitos.
Tipos populares de detecção de falhas de produção moderna
Instrumentos de detecção de falhas não destrutivos extremamente populares incluem: corrente parasita, acústica (ultrassom) e magnética. Existem outros tipos, mas seu uso não é tão difundido, porque o princípio de seu trabalho é um pouco complicado.
Ultrassom (formato acústico)
Um detector de falhas acústicas é comumente entendido como um conjunto de dispositivos de teste não destrutivos semelhantes em sua funcionalidade. Sua ação é baseada nos princípios das ondas acústicas. De acordo com os princípios físicos mais simples, os indicadores básicos de uma onda sonora não podem ser alterados ao se propagar em um microambiente homogêneo. No entanto, se um novo meio bloqueia o caminho da onda, seu comprimento e frequência mudam. Quanto maior a frequência do som, mais preciso será o resultado, portanto, dentre toda a faixa disponível, utiliza-se o ultrassom. O dispositivo ultrassônico emite ondas que penetram no objeto de teste. Se houver cavidades ou inclusões de outros materiais, bem como outros defeitos, a onda invariavelmente os detectará, mostrando isso alterando seus parâmetros.
Os detectores de falhas que operam com base no princípio da ecolocalização são considerados os mais acessíveis e difundidos. A onda entra no objeto e, se nenhum defeito for encontrado, não é refletido, respectivamente, o dispositivo não recebe um feedback e nenhuma violação é registrada. Se a onda voltou, isso indica a presença de falhas. De qualquer forma, o próprio dispositivo é um gerador e um receptor de ultrassom, o que facilita muito as operações de detecção de falhas. O modo de ação do espelho é um pouco como a ecolocalização, mas usa dispositivos separados - este é um gerador e um receptor.A vantagem desse método é que ambos os dispositivos estão localizados no mesmo lado do objeto em estudo, o que simplifica qualitativamente o procedimento de montagem, ajuste e medição. Separadamente, vale a pena mencionar os métodos de análise ultrassônica. O conceito de "som sombra" é usado aqui. Se houver um defeito dentro do objeto, ele contribuirá para o amortecimento instantâneo das vibrações, criando assim uma “sombra”. Esse princípio é baseado no método de sombra de detecção de falhas por meio de ultrassom, no qual o receptor e o transmissor estão no mesmo eixo do som, mas em lados opostos. As desvantagens de tal dispositivo são que, para sua operação completa, devem ser atendidas condições estritas para as dimensões, configuração e nível de rugosidade do objeto que está sendo medido, o que indica uma má unificação do equipamento.
Correntes parasitas e campos magnéticos (formato de correntes parasitas)
Fluxos de vórtice são criados em condutores quando se formam nas imediações de um campo magnético do tipo alternado, com base no fato de que, na presença de defeitos, esses fluxos reproduzem seu próprio campo secundário e os dispositivos de detecção de falhas de correntes parasitas operam. Como resultado, o aparelho descrito de tal princípio de operação forma um campo primário e um campo secundário, que oferece a oportunidade de detectar e identificar deficiências no assunto da pesquisa, é criado como resultado da indução eletromagnética. Já o aparelho recebe um campo secundário, registra seus indicadores e dá um resultado sobre o tipo e a qualidade do defeito.
Esses dispositivos têm um desempenho muito alto e o processo de verificação não leva muito tempo.No entanto, os fluxos de vórtices ocorrem apenas naqueles meios que possuem capacidade condutiva, o que indica a estreita especialização desse aparato.
Formato de partícula magnética
Esta é outra das formas mais comuns. É usado para avaliar soldas, verificar a resistência das camadas protetoras, a confiabilidade das linhas de tubulação, etc. Este método é especialmente valioso para diagnosticar objetos com uma forma geométrica complexa e locais de difícil acesso para verificação.
O princípio de funcionamento deste método é baseado nos parâmetros físicos dos metais magnetizados. Por meio de ímãs permanentes (ou seus análogos) capazes de formar um campo magnético circular/longitudinal, um reagente especial, um pó magnético, é aplicado ao objeto de teste (método úmido/seco). Sob a influência do campo, o pó será combinado nas chamadas cadeias, estruturadas e formando um padrão distinto na forma de linhas onduladas na superfície. A imagem resultante demonstrará claramente o funcionamento do campo, e conhecendo os parâmetros necessários das linhas curvas, você poderá ver onde há discrepâncias e determinar a localização do defeito. Normalmente, uma quantidade particularmente grande de pó se acumula no local do defeito (cavidades, rachaduras). O resultado final é fixado comparando a imagem resultante com um padrão de qualidade.
Outros tipos de detecção de falhas
Novas técnicas aparecem constantemente, quase todos os anos. Ao mesmo tempo, os antigos perdem imediatamente sua antiga popularidade. Muitos dispositivos modernos são altamente especializados e são usados apenas para indústrias específicas.
Por exemplo, os dispositivos fluxgate operam analisando os impulsos que são criados quando ele se move ao longo do objeto.São utilizados na produção de laminados, metalurgia em geral e na inspeção de soldas.
Dispositivos de radiação em operação irradiam objetos com raios alfa, beta, gama e X, bem como os bombardeiam com nêutrons. O resultado é uma imagem muito detalhada do objeto com inomogeneidades e defeitos visíveis. O método é caracterizado pelo alto custo, que é compensado pelo aumento do conteúdo da informação.
Os modelos capilares são projetados para detectar rachaduras e lacunas externas quando expostos a um agente revelador especial. O resultado é avaliado puramente visualmente. O método capilar é usado na construção naval, aviação e engenharia mecânica.
Na indústria de energia, todas as imperfeições nos produtos (que estão sob alta tensão) são detectadas por detectores de falhas eletro-ópticas. Eles podem capturar as menores mudanças nas descargas de partículas de superfície e corona, o que torna possível analisar a operação de um objeto remotamente, sem interromper sua operação.
Preparando-se para o diagnóstico
Antes do início do teste, é necessário limpar a superfície de vestígios de corrosão, materiais de pintura e outros revestimentos. No entanto, não é necessário limpar toda a superfície, basta observar uma folga de 70 centímetros. Desta forma, o objeto estará preparado para diagnóstico, mas ainda seria preferível verificar adicionalmente a permeabilidade da onda ultrassônica. Para fazer isso, você pode usar óleo, graxa, glicerina e outras substâncias líquidas com teor de gordura. Em seguida, você precisará ajustar e calibrar o dispositivo de digitalização para opções específicas. As principais tarefas são:
- Verificação de objetos com espessura inferior a 20 milímetros (é permitido usar as configurações padrão de fábrica);
- Exame de objetos com espessura superior a 20 milímetros (os dados do diagrama ART são adicionados às configurações);
- Diagnóstico da confiabilidade das soldas (calibração complexa com dados do diagrama ART e esclarecimento de outros impulsos complexos serão necessários).
Somente após a conclusão da configuração, você deve prosseguir com as operações de verificação.
Alcançar o mais alto nível de precisão de pesquisa
Para obter a máxima precisão do resultado, a sonda do dispositivo deve ser movida em ziguezague sobre a superfície, enquanto é necessário girar a sonda em torno do eixo em cerca de 10-15%. Se o dispositivo começar a produzir vibrações atípicas, no local detectado é necessário expandir a sonda o máximo possível para determinar com mais precisão a localização da conexão mal feita. A busca deve ser realizada até que seja conhecido o ponto em que o pico da onda será o mais alto. Ao mesmo tempo, deve-se levar em consideração que o equipamento pode retornar o resultado com algum erro, que é consequência da reflexão das ondas das costuras. Em seguida, outros métodos de diagnóstico devem ser aplicados. Se vários métodos diferentes levarem a um único resultado, você poderá corrigir a falha anotando suas coordenadas. Os fabricantes de detectores de falhas confiam nos requisitos das Normas Estaduais e recomendam testar um objeto com pelo menos dois métodos diferentes. Todos os dados obtidos devem ser registrados em um diário ou tabela especial. Assim, você pode eliminar rapidamente o defeito no objeto e agilizar o diagnóstico final, pois todos os pontos problemáticos identificados já são conhecidos.
Defeitos que são detectados por detectores de falhas ultrassônicos com a maior probabilidade
O controle das costuras de soldagem, realizado por meio de dispositivos do tipo em questão, permite obter uma visão clara da situação.Procedimento realizado corretamente pode garantir quase 100% de precisão do resultado. No entanto, existem desvantagens que são bastante difíceis de detectar. Mas há muitos defeitos 100% detectados, e eles incluem:
- Lascas, rachaduras;
- Poros;
- Soldas mal cozidas;
- Laminação de ligas metálicas;
- fístulas;
- Costuras flácidas no início/fim de toda a estrutura;
- Vestígios de corrosão;
- Exclusão mútua em uma junta de dois metais diferentes;
- Desvio de indicadores geométricos no esquema de projeto.
A pesquisa realizada em tipos de metais como:
- Aço,
- Cobre,
- Ferro fundido.
Além disso, os seguintes tipos de suturas estão disponíveis para o diagnóstico de ultrassom:
- em forma de T;
- apartamento;
- transversal;
- Longitudinal;
- Anel.
Vantagens dos detectores de falhas ultrassônicos
Eles podem incluir:
- Maior precisão e coleta acelerada de informações de avaliação;
- O baixo custo do procedimento em si;
- Portabilidade dos equipamentos utilizados, o que permite trabalhar “no campo”;
- A possibilidade de realizar pesquisas sem interromper o funcionamento do objeto diagnosticado;
- Sem risco para soldas, cavidades de tubos e outros substratos sólidos.
Dificuldades de escolha
Os principais parâmetros que exigem muita atenção antes da compra podem ser chamados:
- Faixa de medição;
- Propósito e propósito;
- Desempenho geral;
- Complexidade de montagem/configuração;
- Limites de temperaturas de operação;
- Confiabilidade.
Diferentes modelos têm diferentes faixas de medição, o que significa que alguns instrumentos podem detectar defeitos de até um micrômetro, enquanto outros são limitados a dez milímetros. Tal detalhe desempenha um papel muito importante, por exemplo, na engenharia mecânica, mas para fins de construção, alta precisão é desnecessária.Assim, para esta última indústria, não adianta adquirir um aparelho preciso e caro. Além disso, nos documentos de acompanhamento, o fabricante deve indicar para que tipo de materiais um determinado modelo se destina, bem como quais deficiências ele pode revelar. Separadamente, requisitos especiais podem ser impostos sobre a natureza da superfície, a presença / ausência de camadas protetoras, a forma e as dimensões do item de teste.
O indicador de desempenho determina a velocidade de digitalização e o objeto do procedimento, que pode ser "anexado" a uma unidade de tempo específica. Assim, os modelos fluxgate e de correntes parasitas podem fornecer maior velocidade, mas o processo de magnetização e o trabalho com cada seção separadamente podem levar muito tempo. Separadamente, vale destacar o processo de instalação/montagem/configuração. Dispositivos portáteis de mão que cabem facilmente em uma bolsa serão a melhor solução para o serviço de inspeção de serviço. Dispositivos mais precisos e complexos sempre exigirão tempo adicional de instalação/ajuste. Tendo em vista que os ensaios não destrutivos podem ser realizados tanto em ambientes internos quanto externos (incluindo a estação fria), é necessário determinar os limites das temperaturas de operação. Ao mesmo tempo, você precisa cuidar da possibilidade de trabalhar em ambientes agressivos.
Classificação dos melhores detectores de falhas ultrassônicos para 2025
Segmento de orçamento
3º lugar: "TUD-1 Sonel Ultrasonic Leak and Electrical Discharge Detector"
O modelo pode determinar com precisão o local de despressurização (o local de vazamento de gases/líquidos, o local de perda de vácuo).É utilizado para: controle de suprimento de oxigênio, sistemas automáticos de extinção de incêndio, durante instalação de ar condicionado e ventilação, exame de isoladores em redes de contato, diagnóstico de objetos de desenvolvimento, armazenamento e processamento de derivados de petróleo/gás, busca de pontos de danos aos sistemas de freio em carros, detecção de descargas elétricas em ASUs de baixa tensão a uma distância de até 10 metros e em alta tensão - a uma distância de até 30 metros. Ele funciona com o princípio de registrar a ocorrência de defeitos nos materiais, que é acompanhado por uma mudança brusca na radiação acústica, inclusive na região ultrassônica. O dispositivo converte a radiação em sinais em formas sonoras/gráficas, e o operador corrige os defeitos e toma uma decisão sobre a necessidade de reparos. O modelo funciona sem contato, não sendo necessário desconectar o sujeito da rede elétrica ou desligar o equipamento. O aparelho possui ajuste manual da intensidade do sinal, o que permite que o aparelho seja ajustado às características individuais do operador. A aplicação também é possível em temperaturas negativas até -20 °C. O custo recomendado para redes de varejo é de 32.760 rublos
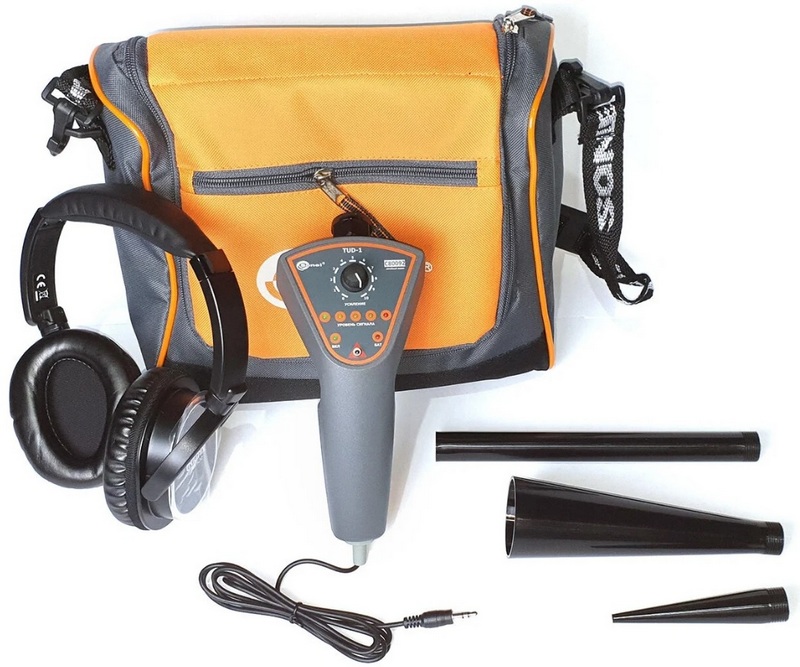
detector de defeitos TUD-1 Detector ultrassônico de vazamento e descarga elétrica Sonel
Vantagens:
- Versatilidade prática;
- Temperaturas de operação suficientes;
- Preço adequado.
Imperfeições:
2º lugar: "Dureza Inatest combinado: ultra-sônico e dinâmico (ultra-sônico Inatest-U com sonda tipo "A" com verificação)"
Este modelo é considerado universal, pois é possível encomendar muitos equipamentos adicionais para ele, ampliando sua funcionalidade. Por exemplo, pode trabalhar com 7 tipos diferentes de sensores para ferro fundido, engrenagens e ranhuras de aço, produtos de metal fino, etc.É possível trabalhar em condições específicas de controle de dureza. Três variantes de sensores para medição de vibrações galvânicas são fornecidas como padrão. O custo recomendado para redes de varejo é de 71.880 rublos.
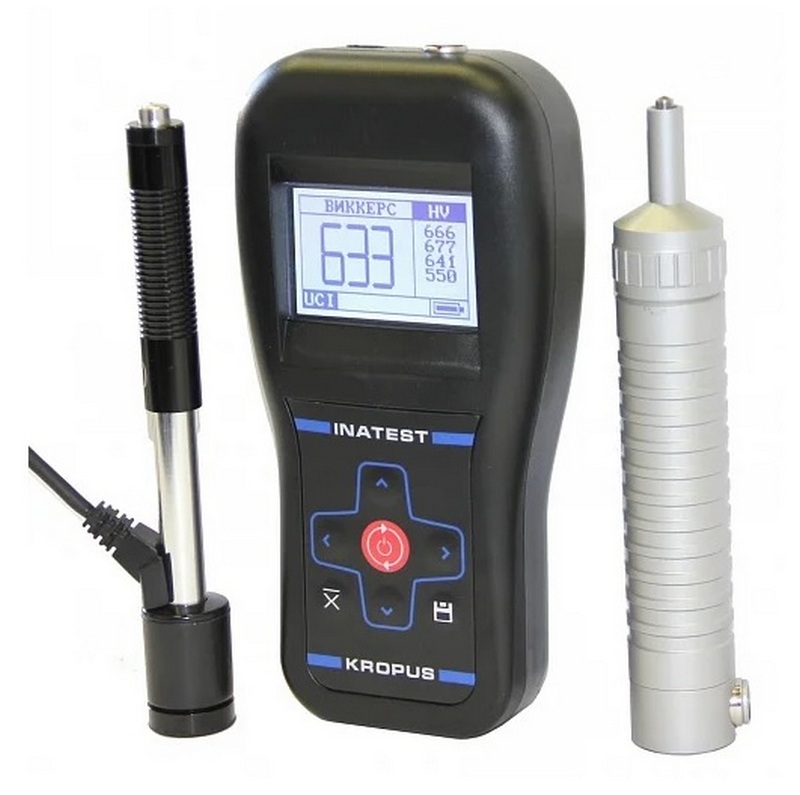
detector de defeitos Dureza combinada Inatest: ultra-sônico e dinâmico (ultra-sônico Inatest-U com sensor tipo “A” com verificação)
Vantagens:
- Possibilidade de adição opcional de sensores;
- Versatilidade;
- Trabalhe em condições especiais.
Imperfeições:
- A necessidade de adquirir componentes adicionais para uma tarefa específica.
1º lugar: "Testador de dureza TVM-UD combinado: ultrassônico e dinâmico (TVM-UD ultrassônico com verificação)"
Outro modelo pré-fabricado, cuja qualidade é confirmada por sua inclusão no registro oficial de instrumentos de medição usados pela empresa estatal Russian Railways. A modificação é considerada universal, mas como padrão possui apenas um tipo de sensor (US). É possível conectar até 10 outros tipos de sensores, até dinâmicos e galvânicos. O custo recomendado para redes de varejo é de 85.511 rublos.
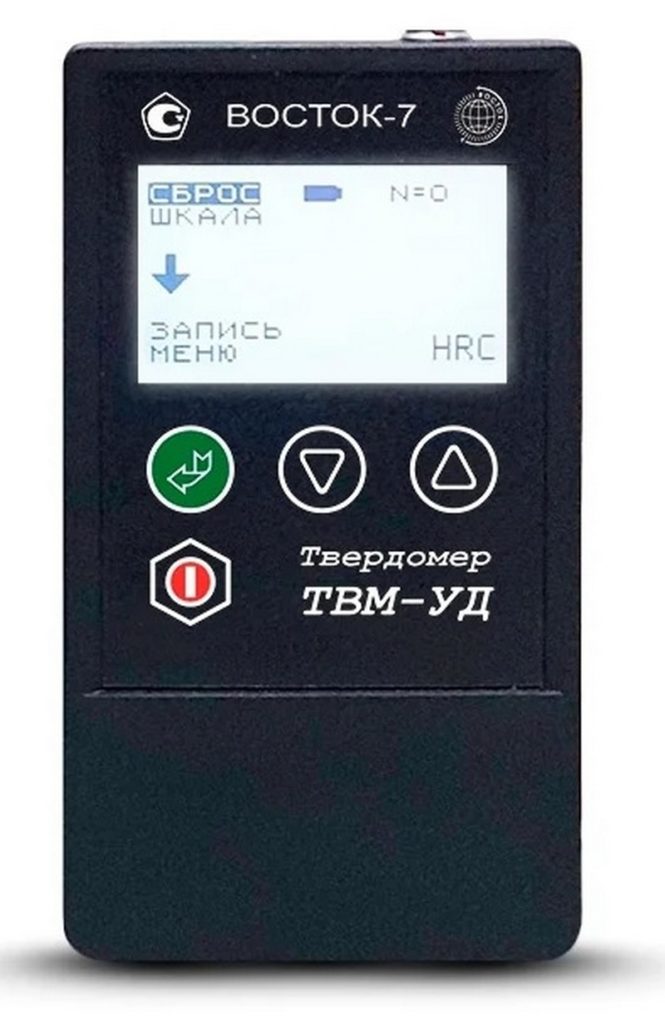
detector de falhas TVM-UD testador de dureza combinado: ultra-sônico e dinâmico (TVM-UD ultra-sônico com verificação)
Vantagens:
- Capacidade de trabalhar com 10 sensores diferentes;
- Tem reconhecimento em nível estadual;
- Modo de operação combinado.
Imperfeições:
Segmento de preço médio
3º lugar: "UKS-MG4S para controlar a resistência de materiais de construção e rochas (UKS-MG4 com verificação)"
Este modelo avançado em sua configuração básica utiliza apenas o método de bombeamento de ondas de superfície para determinar a resistência do concreto e produtos de concreto armado, tijolos e pedras de silicato.Possui design monobloco, que é uma unidade eletrônica com conversores em uma única carcaça. Caracterizado por um alto nível de precisão. O custo recomendado para redes de varejo é de 92.000 rublos.
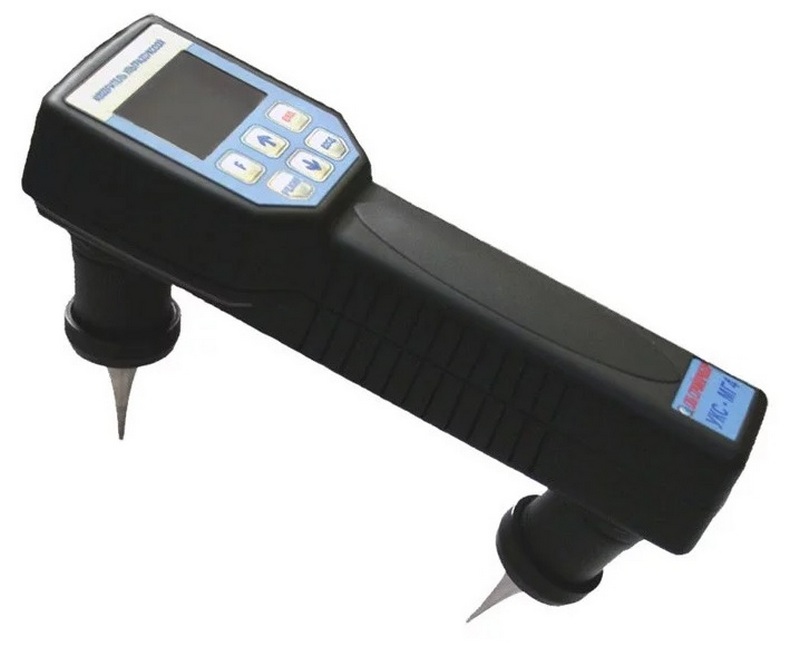
detector de defeitos UKS-MG4S para testar a resistência de materiais de construção e rochas (UKS-MG4 com verificação)
Vantagens:
- Especialização estreita (construção);
- Execução na forma de monobloco;
- Nível de precisão suficiente.
Imperfeições:
2º lugar: "PULSAR-2M TFT (verificado)"
O dispositivo excelente que se caracteriza pela alta exatidão da análise fora transportada. Tem um design em forma de monobloco e é perfeito para os departamentos de testes não destrutivos em serviço. É conveniente carregá-lo mesmo no bolso, pois possui pequenas dimensões. A tela é colorida e todos os controles são intuitivos. Há um bloco de memória para armazenar uma grande quantidade de resultados. O custo recomendado para redes de varejo é de 138.000 rublos.
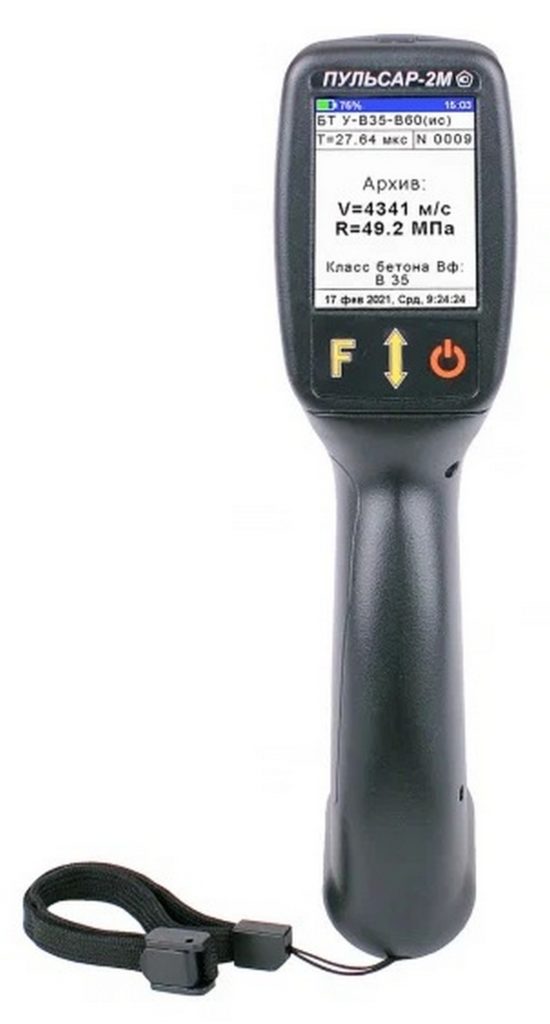
detector de falhas PULSAR-2M TFT (com verificação)
Vantagens:
- A alta funcionalidade corresponde ao preço declarado;
- Máxima portabilidade;
- Exibição em cores.
Imperfeições:
1º lugar: "PULSAR-2.1 (verificado)"
Amostra muito cara e multifuncional. Ele pode ser usado em uma variedade de aplicações, desde construção, onde são necessários resultados de precisão média, até engenharia de alta precisão, onde são necessárias análises de até micrômetros. O kit vem com todos os tipos possíveis de sensores. O custo recomendado para redes de varejo é de 140.000 rublos.
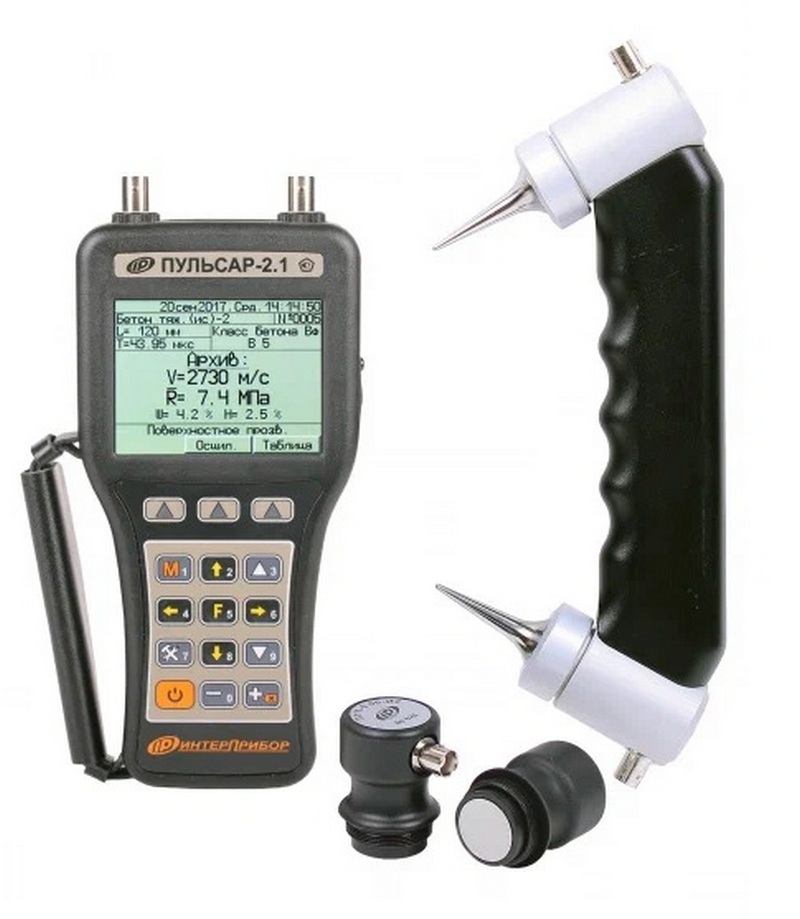
detector de falhas PULSAR-2.1 (com verificação)
Vantagens:
- Relação adequada de equipamentos e preço;
- Amplo escopo de uso;
- Precisão melhorada.
Imperfeições:
Classe Premium
2º lugar: "Emissor submersível SG-18 28kHz 900W com gerador"
Este dispositivo foi projetado para diagnosticar tubulações com qualquer diâmetro, é um equipamento estacionário de alta precisão e é usado para controlar a qualidade do metal laminado em oficinas. Especialmente bem, suas sondas lidam com tubos de geometria irregular e com diâmetro decrescente/aumentando ao longo de todo o comprimento da linha. O kit inclui: plataforma, gerador, sonda de alta frequência, estojo de armazenamento. O custo recomendado para redes de varejo é de 170.000 rublos.
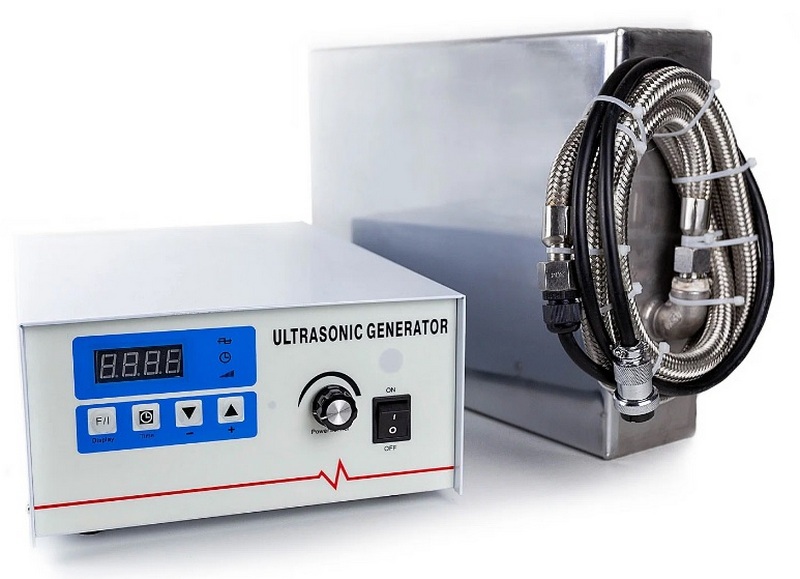
detector de falhas Emissor submersível SG-18 28kHz 900W com gerador
Vantagens:
- Maior precisão;
- Colocação estacionária;
- Capacidade de trabalhar com objetos não padronizados;
- Garantia de um ano.
Imperfeições:
- Escopo limitado (apenas industrial).
1º lugar: "Dispositivo ultrassônico PULSAR-2.2 (com verificação)"
A modificação mais recente e moderna da popular marca russa de equipamentos. O software da versão final está instalado nele, agora é possível exibir gráficos de teste em dinâmica. O kit inclui todos os sensores mais comuns, o equipamento tem pequenas dimensões. O custo recomendado para redes de varejo é de 222.000 rublos.
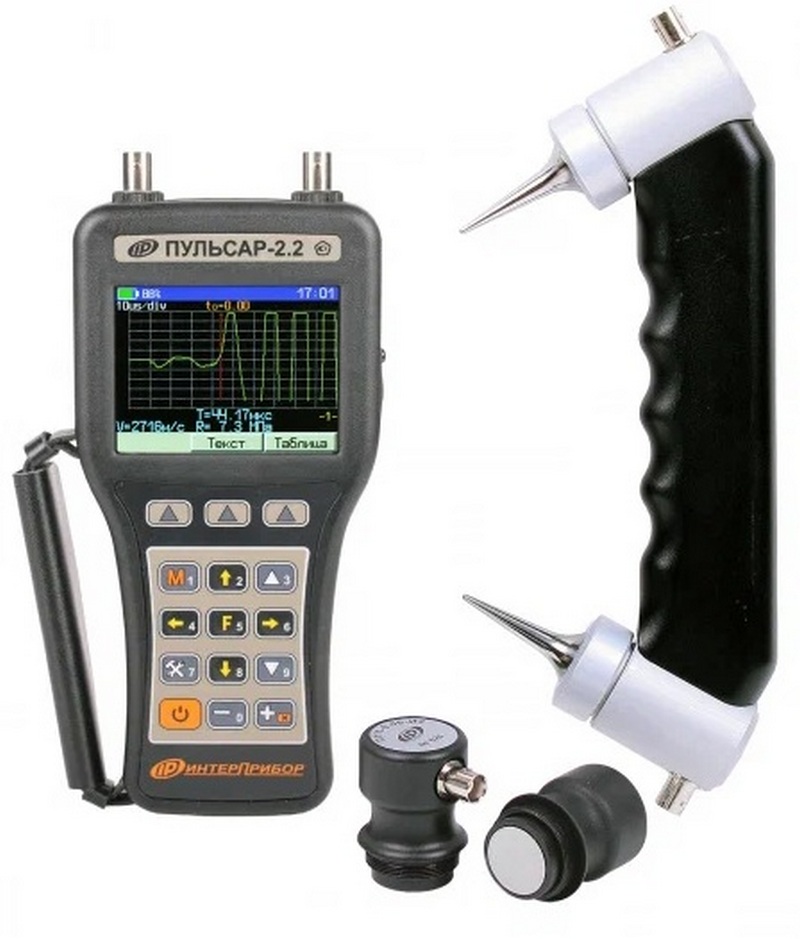
detector de falhas Dispositivo ultrassônico PULSAR-2.2 (com verificação)
Vantagens:
- Versão mais recente do software;
- Bons equipamentos;
- Tamanhos pequenos.
Imperfeições:
Conclusão
Vale sempre lembrar que os equipamentos de alta precisão em questão em termos de peso, dimensões, tipo de alimentação, métodos de detecção de defeitos, resistência a vibrações devem atender aos requisitos da Norma Estadual nº 23049 de 1984.Além disso, qualquer modelo deve ter um mínimo específico de blocos de trabalho com os quais você pode realizar as operações mais padrão.