Defektoskop ultradźwiękowy to sprzęt przeznaczony do wykrywania wad obiektu bez uszkadzania jego integralności. Deformacje wykrywane są poprzez oddziaływanie fal ultradźwiękowych na obiekt. Sprzęt cieszy się dużym zainteresowaniem, ponieważ sposób jego działania jako jedyny pozwala na dostarczenie najdokładniejszych wyników diagnostycznych bez demontażu obiektu badań.
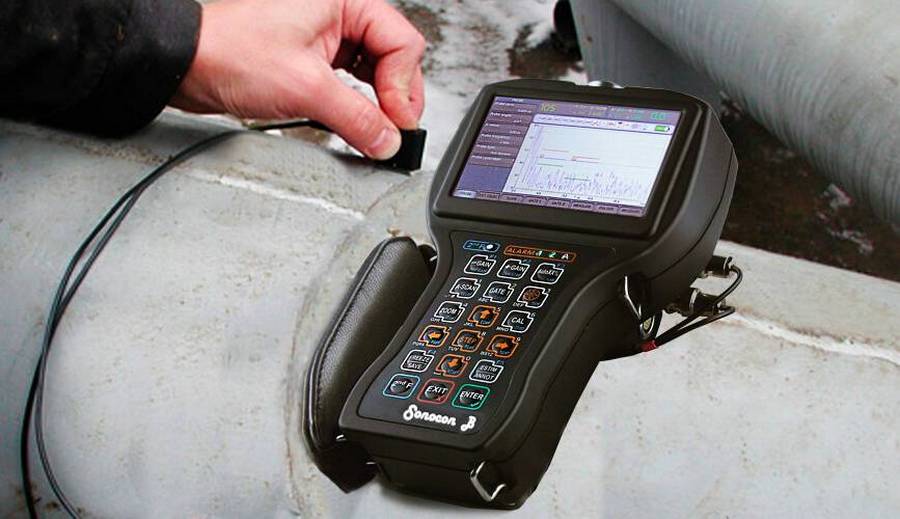
Defektoskop ultradźwiękowy: informacje ogólne
Ultradźwięki przenikają przez warstwę litego żelaza i są w stanie wykryć obecność najmniejszych pęknięć, które mogą znajdować się wewnątrz obiektu. Urządzenie będzie w stanie z dużą dokładnością wykryć defekt na głębokości od 5 do 50 milimetrów. Rozważany sprzęt może mieć różne poziomy czułości. Wskaźnik ten zależy od wielkości i wymiarów wykrytej wady. Zakres urządzenia jest bardzo szeroki, ale najczęściej służą one do określenia jakości wytwarzanych metali.Urządzenia posiadają intuicyjną obsługę, zapewniają zunifikowaną i wydajną obsługę oraz charakteryzują się zwiększoną dokładnością, co pozwala na uzyskanie wysokiej jakości wyników oraz terminowe wykrywanie i korygowanie różnych wad produkcyjnych.
Zasada kontroli ultradźwiękowej
Rozważany typ aparatu jest zwykle używany do kontroli poziomu wytrzymałości na spoiny. W tym przypadku urządzenie podczas pracy działa w następujący sposób: określone fale akustyczne kierowane są na blachę, powodując drgania obudowy. Mogą być następujących typów:
- Naddźwiękowy;
- ultradźwiękowy;
- Dźwięk standardowy;
- Infradźwiękowy.
Podczas przechodzenia ultradźwięku przestrzeń, przez którą się rozchodzi, tworzy równomierne drgania względem punktu spoczynku. W przypadku ciał stałych mogą wystąpić drgania poprzeczne/wzdłużne, co pozwala kontrolować jakość spoin z maksymalną dokładnością. Szybkość propagacji i dostarczania opisywanych fal jest bezpośrednio zależna od siły/środowiska wewnętrznego badanego obiektu. Intensywność fal można regulować. W miarę rozchodzenia się fali jej siła będzie stopniowo zanikać. Na podstawie kontroli szybkości tego wymierania będzie można ocenić siłę szwu. Urządzenie natomiast wyświetli współczynnik tłumienia ultradźwięków, tworząc go na podstawie stopnia absorpcji i rozpraszania. Ostateczna dokładność jest bardzo wysoka, dzięki czemu można uzyskać konkretne pomysły na temat jakości metalu, wytrzymałości szwu i braku / obecności innych wad.
Popularne typy nowoczesnego wykrywania wad produkcyjnych
Do niezwykle popularnych defektoskopów nieniszczących należą: prądy wirowe, akustyczne (ultradźwięki) i magnetyczne. Istnieją inne typy, ale ich zastosowanie nie jest tak powszechne, ponieważ zasada ich działania jest nieco skomplikowana.
USG (format akustyczny)
Przez defektoskop akustyczny powszechnie rozumie się zestaw urządzeń do badań nieniszczących o podobnej funkcjonalności. Ich działanie opiera się na zasadach fal akustycznych. Zgodnie z najprostszymi zasadami fizycznymi, podstawowych wskaźników fali dźwiękowej nie można zmienić podczas propagacji w jednorodnym mikrośrodowisku. Jeśli jednak nowe medium blokuje drogę fali, zmienia się jej długość i częstotliwość. Im wyższa częstotliwość dźwięku, tym dokładniejszy będzie wynik, dlatego w całym dostępnym zakresie stosuje się ultradźwięki. Urządzenie ultradźwiękowe emituje fale, które penetrują badany obiekt. Jeśli pojawią się ubytki lub wtrącenia innych materiałów, a także inne defekty, to fala niezmiennie je wykryje, pokazując to poprzez zmianę swoich parametrów.
Za najbardziej dostępne i rozpowszechnione uważane są defektoskopy działające na zasadzie echolokacji. Fala wchodzi do obiektu i, jeśli nie zostaną znalezione żadne defekty, nie zostanie odbita, odpowiednio urządzenie nie otrzymuje informacji zwrotnej i nie rejestruje się żadnych naruszeń. Jeśli fala wróciła, oznacza to obecność wad. W każdym razie samo urządzenie jest zarówno generatorem, jak i odbiornikiem ultradźwięków, co znacznie ułatwia operacje wykrywania wad. Tryb działania lustrzanego przypomina trochę echolokację, ale wykorzystuje oddzielne urządzenia - to generator i odbiornik.Zaletą tej metody jest to, że oba urządzenia znajdują się po tej samej stronie badanego obiektu, co jakościowo upraszcza procedurę ustawiania, regulacji i wykonywania pomiarów. Osobno warto wspomnieć o metodach analizy ultradźwiękowej. Zastosowano tu pojęcie „cienia dźwiękowego”. Jeśli wewnątrz obiektu występuje defekt, przyczyni się to do natychmiastowego tłumienia drgań, tworząc w ten sposób „cień”. Zasada ta opiera się na metodzie cieniowania wykrywania wad za pomocą ultradźwięków, w której odbiornik i nadajnik znajdują się na tej samej osi dźwięku, ale po przeciwnych stronach. Wadą takiego urządzenia jest to, że dla jego pełnej pracy muszą być spełnione surowe warunki dotyczące wymiarów, konfiguracji i poziomu chropowatości mierzonego obiektu, co wskazuje na słabą unifikację sprzętu.
Prądy wirowe i pola magnetyczne (format prądów wirowych)
Przepływy wirowe powstają w przewodnikach podczas formowania się w bezpośrednim sąsiedztwie pola magnetycznego typu przemiennego, w oparciu o fakt, że w przypadku defektów przepływy te odtwarzają własne pole wtórne i działają urządzenia do wykrywania wad wiroprądowych. W rezultacie opisana aparatura o takiej zasadzie działania tworzy pole pierwotne, a w wyniku indukcji elektromagnetycznej powstaje pole wtórne, które daje możliwość wykrycia i zidentyfikowania niedociągnięć w przedmiocie badań. Urządzenie natomiast otrzymuje pole wtórne, rejestruje jego wskaźniki i podaje wynik o rodzaju i jakości wady.
Takie urządzenia mają bardzo wysoką wydajność, a proces weryfikacji nie zajmuje dużo czasu.Niemniej jednak przepływy wirowe występują tylko w tych mediach, które mają zdolność przewodzenia, co wskazuje na wąską specjalizację tego aparatu.
Format cząstek magnetycznych
To kolejny z najczęstszych sposobów. Służy do oceny spoin, sprawdzania wytrzymałości warstw ochronnych, niezawodności rurociągów itp. Metoda ta jest szczególnie cenna przy diagnozowaniu obiektów o złożonym kształcie geometrycznym oraz miejsc trudno dostępnych do weryfikacji.
Zasada działania tej metody opiera się na parametrach fizycznych namagnesowanych metali. Za pomocą magnesów trwałych (lub ich analogów) zdolnych do wytworzenia okrągłego/wzdłużnego pola magnetycznego na badany przedmiot nakładany jest specjalny odczynnik, proszek magnetyczny (metoda mokra/sucha). Pod wpływem pola proszek połączy się w tzw. łańcuszki, ustrukturyzowane i uformują wyraźny wzór w postaci falistych linii na powierzchni. Powstały obraz wyraźnie zademonstruje działanie pola, a znając niezbędne parametry zakrzywionych linii, możesz zobaczyć, gdzie występują rozbieżności i określić lokalizację wady. Zwykle w miejscu ubytku (ubytków, pęknięć) gromadzi się szczególnie duża ilość proszku. Ostateczny wynik ustala się, porównując wynikowy obraz ze standardem jakości.
Inne rodzaje wykrywania wad
Nowe techniki pojawiają się nieustannie, prawie co roku. Jednocześnie stare natychmiast tracą swoją dawną popularność. Wiele nowoczesnych urządzeń jest wysoce wyspecjalizowanych i wykorzystywanych tylko dla określonych branż.
Na przykład urządzenia fluxgate działają na podstawie analizy impulsów, które powstają, gdy porusza się wzdłuż obiektu.Stosowane są w produkcji wyrobów walcowanych, w metalurgii ogólnej oraz przy kontroli spoin.
Działające urządzenia radiacyjne naświetlają obiekty promieniowaniem alfa, beta, gamma i rentgenowskim, a także bombardują je neutronami. Rezultatem jest bardzo szczegółowy obraz obiektu z widocznymi niejednorodnościami i defektami. Metoda charakteryzuje się wysokim kosztem, który jest rekompensowany zwiększoną zawartością informacji.
Modele kapilarne są przeznaczone do wykrywania zewnętrznych pęknięć i szczelin po ekspozycji na określony środek wywołujący. Wynik oceniany jest czysto wizualnie. Metodę kapilarną stosuje się w przemyśle stoczniowym, lotnictwie i inżynierii mechanicznej.
W energetyce wszelkie niedoskonałości produktów (które są pod wysokim napięciem) są wykrywane przez defektoskopy elektronowo-optyczne. Potrafią uchwycić najmniejsze zmiany w wyładowaniach powierzchniowo-cząstkowych i koronowych, co umożliwia zdalną analizę pracy obiektu bez zatrzymywania jego pracy.
Przygotowanie do diagnostyki
Przed rozpoczęciem testu konieczne jest oczyszczenie powierzchni ze śladów korozji, materiałów lakierniczych i innych powłok. Nie jest jednak konieczne czyszczenie całej powierzchni, wystarczy obserwować szczelinę 70 centymetrów. W takiej formie obiekt będzie przygotowany do diagnostyki, ale nadal lepiej byłoby dodatkowo sprawdzić drożność fali ultradźwiękowej. Aby to zrobić, możesz użyć oleju, smaru, gliceryny i innych płynnych substancji o zawartości tłuszczu. Następnie musisz dostosować i skalibrować urządzenie skanujące pod kątem określonych opcji. Główne zadania to:
- Sprawdzanie obiektów o grubości mniejszej niż 20 milimetrów (dozwolone jest użycie domyślnych ustawień fabrycznych);
- Badanie obiektów o grubości większej niż 20 milimetrów (dane z diagramu ART są dodawane do ustawień);
- Diagnoza niezawodności spoin (wymagana będzie złożona kalibracja z danymi ze schematu ART i wyjaśnienie innych złożonych impulsów).
Dopiero po zakończeniu konfiguracji należy przystąpić do operacji weryfikacji.
Osiągnięcie najwyższego poziomu dokładności badań
W celu uzyskania maksymalnej dokładności wyniku sonda urządzenia musi być przesuwana w sposób zygzakowaty po powierzchni, przy czym konieczne jest obracanie sondy wokół osi o około 10-15%. Jeśli urządzenie zacznie wytwarzać nietypowe wibracje, to w wykrytym miejscu należy maksymalnie rozszerzyć sondę, aby dokładniej określić lokalizację źle wykonanego połączenia. Poszukiwania należy prowadzić do momentu, w którym znany będzie punkt, w którym szczyt fali będzie najwyższy. Jednocześnie należy wziąć pod uwagę, że sprzęt może zwrócić wynik z pewnym błędem, co jest konsekwencją odbicia fali od szwów. Następnie należy zastosować inne metody diagnostyczne. Jeśli kilka różnych metod prowadzi do jednego wyniku, możesz naprawić usterkę, zapisując jej współrzędne. Producenci defektoskopów opierają się na wymaganiach norm państwowych i zalecają testowanie jednego obiektu co najmniej dwoma różnymi metodami. Wszystkie uzyskane dane muszą być zapisywane w specjalnym dzienniku lub tabeli. Dzięki temu można szybko wyeliminować usterkę w obiekcie i przyspieszyć ostateczną diagnozę, ponieważ wszystkie zidentyfikowane punkty problemowe są już znane.
Defekty wykrywane przez defektoskopy ultradźwiękowe z najwyższym prawdopodobieństwem
Kontrola szwów spawalniczych, realizowana za pomocą urządzeń tego typu, pozwala uzyskać jasny obraz sytuacji.Prawidłowo wykonany zabieg może zagwarantować prawie 100% dokładność wyniku. Istnieją jednak wady, które są dość trudne do wykrycia. Ale jest wiele wykrytych 100% wad, a wśród nich:
- Odpryski, pęknięcia;
- pory;
- Spoiny niedogotowane;
- Laminowanie stopów metali;
- przetoki;
- Zwisające szwy na początku / końcu całej konstrukcji;
- Ślady korozji;
- Wzajemne wykluczenie w jednym połączeniu dwóch różnych metali;
- Odchylenie od wskaźników geometrycznych w schemacie projektowym.
Badania prowadzone na takich rodzajach metali jak:
- Stal,
- Miedź,
- Żeliwo.
Dostępne są również następujące rodzaje szwów do diagnozowania USG:
- w kształcie litery T;
- mieszkanie;
- poprzeczny;
- Wzdłużny;
- Dzwonić.
Zalety defektoskopów ultradźwiękowych
Mogą obejmować:
- Zwiększona dokładność i przyspieszone zbieranie informacji dotyczących oceny;
- Niski koszt samej procedury;
- Przenośność używanego sprzętu, która umożliwia pracę „w terenie”;
- Możliwość prowadzenia badań bez przerywania pracy diagnozowanego obiektu;
- Brak ryzyka dla spawów, wnęk rur i innych stałych podłoży.
Trudności z wyborem
Główne parametry, które wymagają szczególnej uwagi przed zakupem, można nazwać:
- Zakres pomiaru;
- Cel i cel;
- Całkowita wydajność;
- złożoność montażu/konfiguracji;
- Granice temperatur roboczych;
- Niezawodność.
Różne modele mają różne zakresy pomiarowe, co oznacza, że niektóre przyrządy mogą wykrywać defekty do jednego mikrometra, podczas gdy inne są ograniczone do dziesięciu milimetrów. Taki detal odgrywa bardzo ważną rolę np. w inżynierii mechanicznej, ale do celów konstrukcyjnych nie jest konieczna wysoka dokładność.Tak więc dla tej ostatniej branży nie ma sensu kupować dokładnego i drogiego urządzenia. Ponadto w dokumentach towarzyszących producent musi wskazać, do jakiego rodzaju materiałów jest przeznaczony dany model, a także jakie niedociągnięcia może ujawnić. Oddzielnie można nałożyć specjalne wymagania na rodzaj powierzchni, obecność / brak warstw ochronnych, kształt i wymiary badanego przedmiotu.
Wskaźnik wydajności określa szybkość skanowania oraz przedmiot zabiegu, który można „przypiąć” do określonej jednostki czasu. Tak więc modele fluxgate i wiroprądowe mogą zapewnić zwiększoną prędkość, ale proces magnesowania i pracy z każdą sekcją osobno może zająć dość dużo czasu. Osobno warto wspomnieć o procesie instalacji/montażu/konfiguracji. Ręczne przenośne urządzenia, które z łatwością mieszczą się w torbie, będą najlepszym rozwiązaniem dla służby kontrolnej. Bardziej precyzyjne i złożone urządzenia zawsze będą wymagały dodatkowego czasu na instalację/regulację. W związku z tym, że badania nieniszczące mogą być prowadzone zarówno w pomieszczeniach, jak i na zewnątrz (w tym w zimnych porach roku), konieczne jest określenie granic temperatur pracy. Jednocześnie trzeba zadbać o możliwość pracy w agresywnych środowiskach.
Ocena najlepszych defektoskopów ultradźwiękowych na rok 2025
Segment budżetu
III miejsce: „Ultradźwiękowy czujnik nieszczelności i wyładowań elektrycznych TUD-1 Sonel”
Model może dokładnie określić miejsce rozhermetyzowania (miejsce wycieku gazów/cieczy, miejsce utraty próżni).Służy do: kontroli dopływu tlenu, automatycznych systemów gaśniczych, podczas montażu klimatyzacji i wentylacji, badania izolatorów w sieciach stykowych, diagnostyki obiektów zabudowy, magazynowania i przetwarzania produktów ropopochodnych/gazowych, poszukiwania punktów uszkodzenia układów hamulcowych w samochodach, wykrywanie wyładowań elektrycznych w niskonapięciowych ASU z odległości do 10 metrów, a w wysokonapięciowych - z odległości do 30 metrów. Działa na zasadzie rejestracji występowania defektów w materiałach, czemu towarzyszy gwałtowna zmiana promieniowania akustycznego, także w obszarze ultradźwiękowym. Urządzenie zamienia promieniowanie na sygnały w postaci dźwiękowej/graficznej, a operator naprawia usterki i podejmuje decyzję o konieczności naprawy. Model działa bezdotykowo i nie wymaga odłączania przedmiotu od zasilania ani zatrzymywania sprzętu. Urządzenie posiada ręczną regulację siły sygnału, co pozwala na dostosowanie urządzenia do indywidualnych cech operatora. Możliwa jest również aplikacja w temperaturach ujemnych do -20 °C. Zalecany koszt dla sieci handlowych to 32 760 rubli
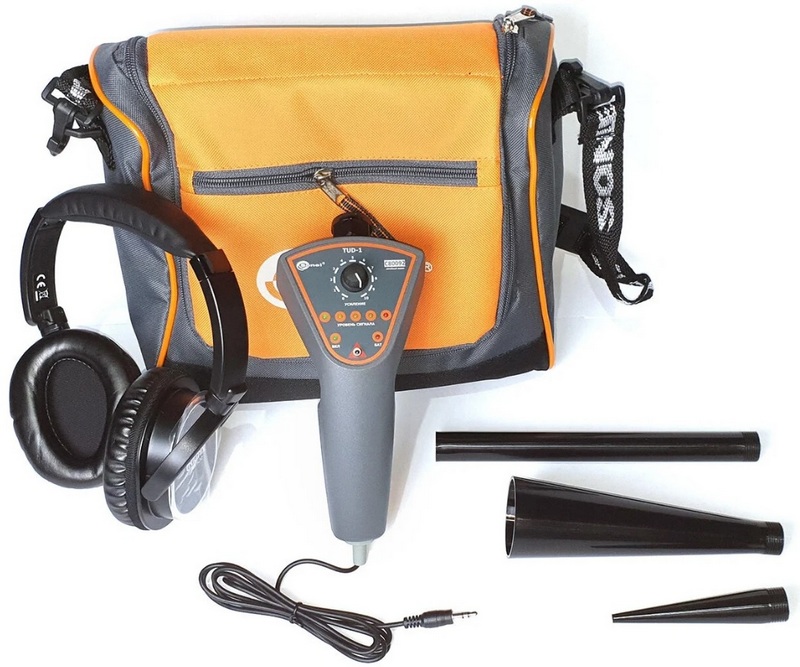
defektoskop TUD-1 Ultradźwiękowy wykrywacz nieszczelności i wyładowań elektrycznych Sonel
Zalety:
- Praktyczna wszechstronność;
- Wystarczające temperatury pracy;
- Adekwatna cena.
Wady:
II miejsce: „Twardościomierz Inatest połączony: ultradźwiękowy i dynamiczny (ultradźwiękowy Inatest-U z sondą typu „A” z weryfikacją)”
Model ten uważany jest za uniwersalny, ponieważ można do niego zamówić wiele dodatkowego wyposażenia, rozszerzającego jego funkcjonalność. Na przykład może współpracować z 7 różnymi typami czujników do żeliwa, stalowych kół zębatych i rowków, cienkich wyrobów metalowych itp.Możliwa jest praca w określonych warunkach kontroli twardości. Standardowo dostarczane są trzy warianty czujników do pomiaru drgań galwanicznych. Zalecany koszt dla sieci handlowych to 71 880 rubli.
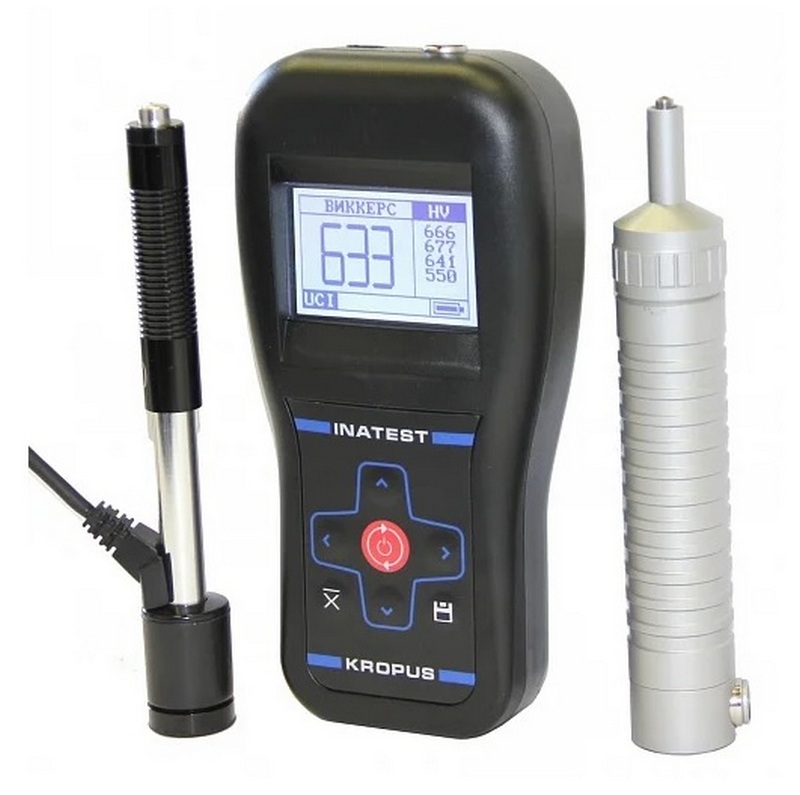
defektoskop Inatest kombinowany twardościomierz: ultradźwiękowy i dynamiczny (ultradźwiękowy Inatest-U z czujnikiem typu „A” z weryfikacją)
Zalety:
- Możliwość opcjonalnego dodania czujników;
- Wszechstronność;
- Pracuj w specjalnych warunkach.
Wady:
- Konieczność zakupu dodatkowych komponentów do konkretnego zadania.
I miejsce: „Twardościomierz TVM-UD łączony: ultradźwiękowy i dynamiczny (ultradźwiękowy TVM-UD z weryfikacją)”
Kolejny prefabrykowany model, którego jakość potwierdza wpis do oficjalnego rejestru przyrządów pomiarowych wykorzystywanych przez państwowe przedsiębiorstwo Koleje Rosyjskie. Modyfikacja jest uważana za uniwersalną, ale standardowo posiada tylko jeden typ czujnika (US). Możliwe jest podłączenie do 10 innych typów czujników, do dynamicznych i galwanicznych. Zalecany koszt dla sieci handlowych to 85 511 rubli.
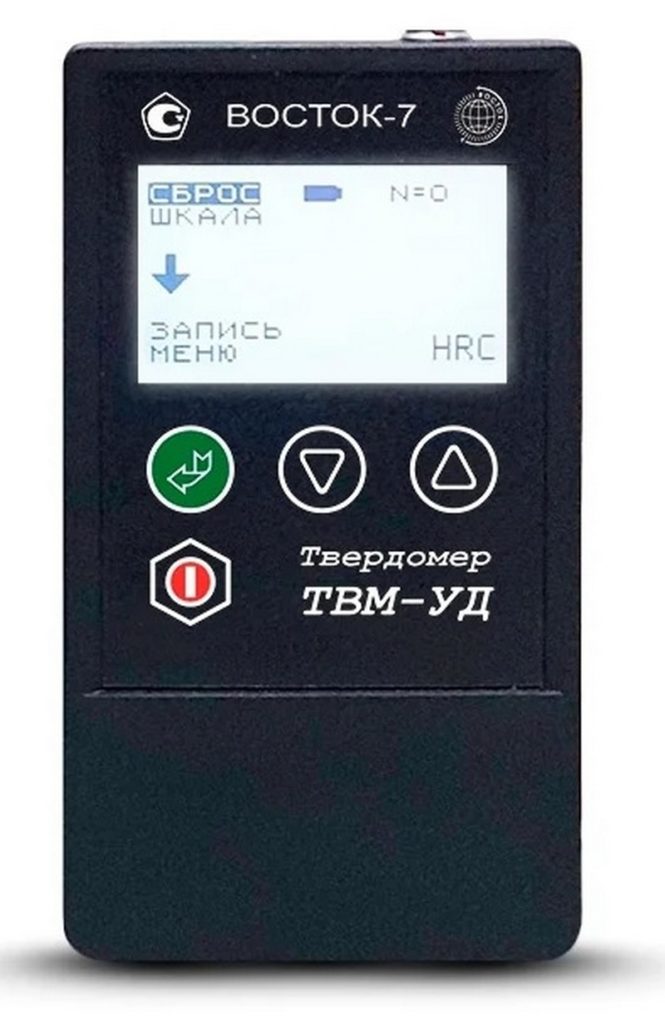
defektoskop TVM-UD twardościomierz kombinowany: ultradźwiękowy i dynamiczny (ultradźwiękowy TVM-UD z weryfikacją)
Zalety:
- Możliwość pracy z 10 różnymi czujnikami;
- Posiada uznanie na szczeblu państwowym;
- Połączony tryb pracy.
Wady:
Średni segment cenowy
III miejsce: „UKS-MG4S do kontroli wytrzymałości materiałów budowlanych i skał (UKS-MG4 z weryfikacją)”
Ten zaawansowany model w podstawowej konfiguracji wykorzystuje wyłącznie metodę pompowania fal powierzchniowych do określania wytrzymałości wyrobów betonowych i żelbetowych, cegieł i kamieni silikatowych.Ma konstrukcję monoblokową, która jest jednostką elektroniczną z przetwornikami w jednej obudowie. Charakteryzuje się wysokim poziomem dokładności. Zalecany koszt dla sieci handlowych to 92 000 rubli.
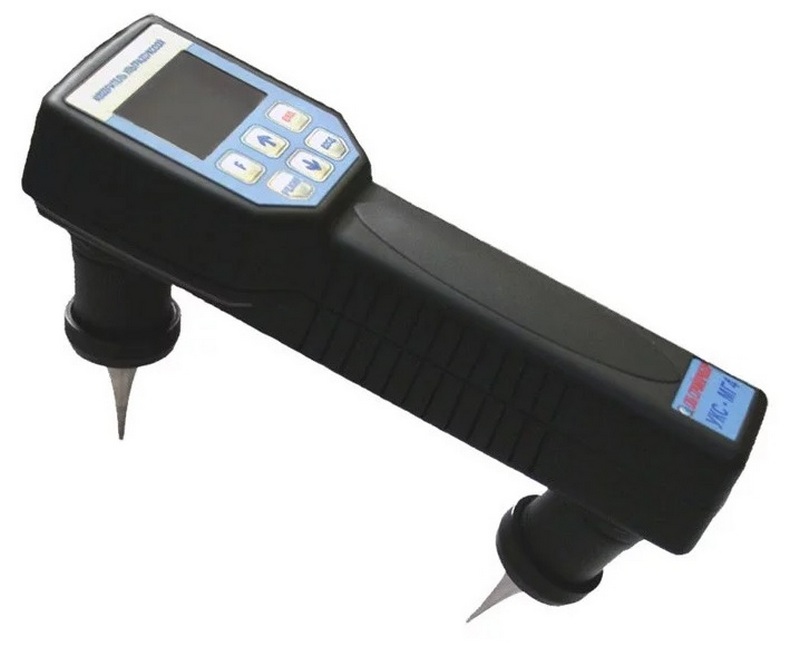
defektoskop UKS-MG4S do badania wytrzymałości materiałów budowlanych i skał (UKS-MG4 z weryfikacją)
Zalety:
- Wąska specjalizacja (budownictwo);
- Wykonanie w formie monobloku;
- Wystarczający poziom dokładności.
Wady:
2 miejsce: „PULSAR-2M TFT (zweryfikowany)”
Doskonałe urządzenie charakteryzujące się dużą dokładnością przeprowadzonej analizy. Ma konstrukcję w postaci monobloku i doskonale sprawdza się w działach badań nieniszczących na służbie. Wygodnie nosi się go nawet w kieszeni, ponieważ ma niewielkie wymiary. Wyświetlacz jest kolorowy, a wszystkie elementy sterujące są intuicyjne. Istnieje blok pamięci do przechowywania dużej ilości wyników. Zalecany koszt dla sieci handlowych to 138 000 rubli.
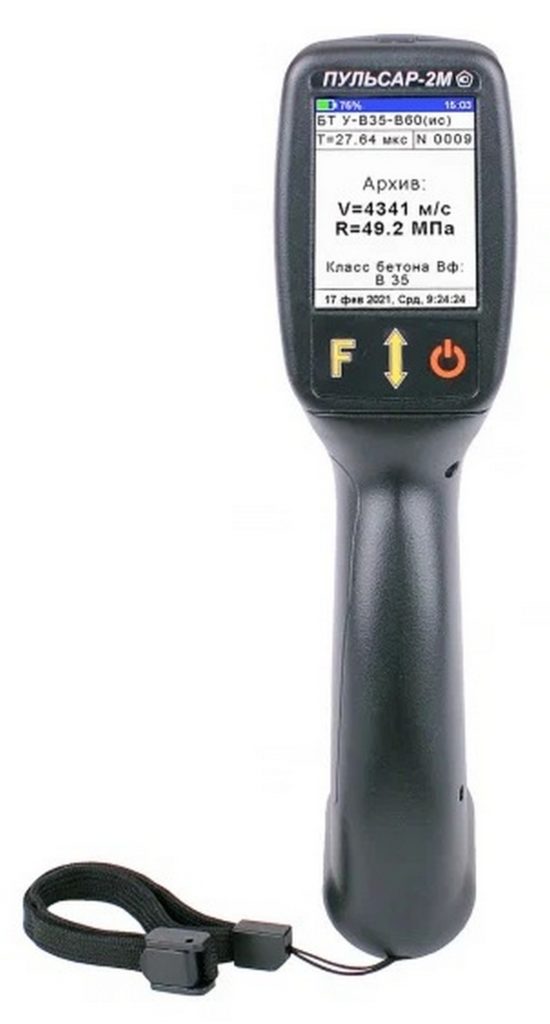
defektoskop PULSAR-2M TFT (z weryfikacją)
Zalety:
- Wysoka funkcjonalność odpowiada zadeklarowanej cenie;
- Maksymalna przenośność;
- Kolorowy wyświetlacz.
Wady:
1 miejsce: „PULSAR-2.1 (zweryfikowany)”
Bardzo droga i wielofunkcyjna próbka. Może być używany w różnych zastosowaniach, od budownictwa, gdzie wymagane są wyniki o średniej precyzji, do inżynierii o wysokiej precyzji, gdzie potrzebne są analizy z dokładnością do mikrometrów. Zestaw zawiera wszystkie możliwe typy czujników. Zalecany koszt dla sieci handlowych to 140 000 rubli.
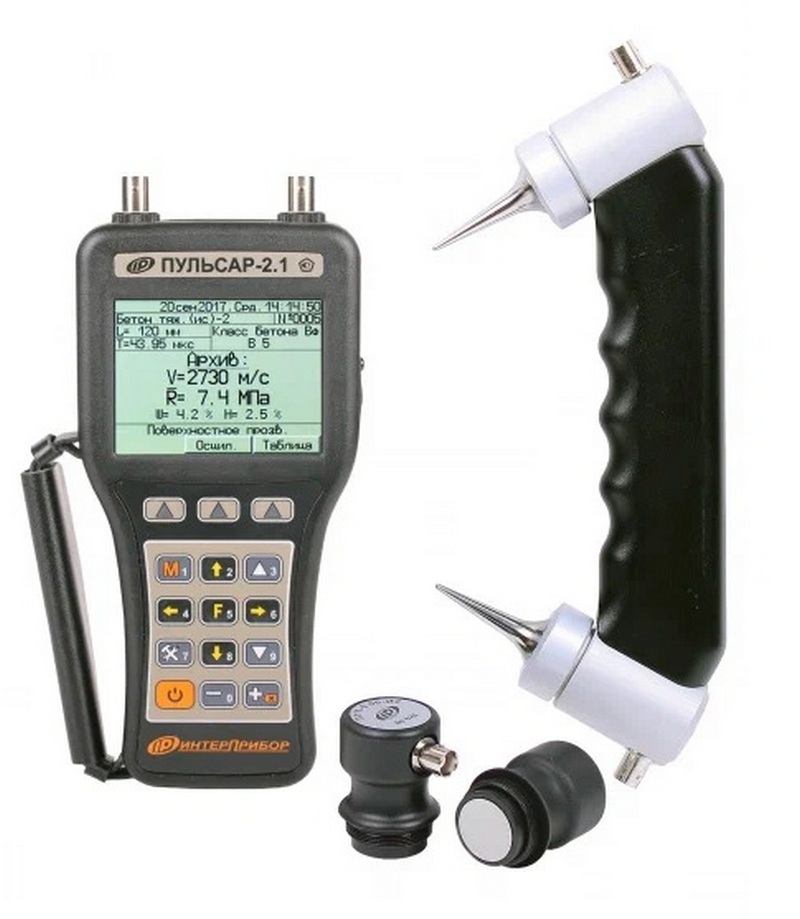
defektoskop PULSAR-2.1 (z weryfikacją)
Zalety:
- Odpowiedni stosunek wyposażenia i ceny;
- Szeroki zakres zastosowania;
- Poprawiona celność.
Wady:
Klasa premium
II miejsce: „Nadajnik zatapialny SG-18 28kHz 900W z generatorem”
Urządzenie przeznaczone jest do diagnozowania rurociągów o dowolnej średnicy, jest wysoce precyzyjnym sprzętem stacjonarnym i służy do kontroli jakości walcowanego metalu w warsztatach. Szczególnie dobrze jej sondy radzą sobie z rurami o nieregularnej geometrii i malejącej/rosnącej średnicy na całej długości linii. W skład zestawu wchodzą: platforma, generator, sonda wysokiej częstotliwości, walizka do przechowywania. Zalecany koszt dla sieci handlowych to 170 000 rubli.
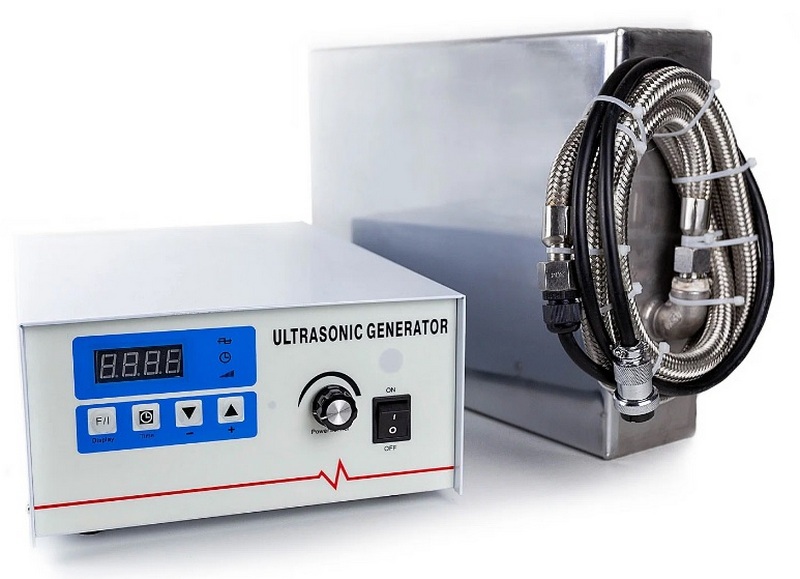
defektoskop Emiter zanurzeniowy SG-18 28kHz 900W z generatorem
Zalety:
- Zwiększona dokładność;
- Stacjonarne umieszczenie;
- Umiejętność pracy z niestandardowymi obiektami;
- Roczna gwarancja.
Wady:
- Ograniczony (tylko przemysłowy) zakres.
I miejsce: „Urządzenie ultradźwiękowe PULSAR-2.2 (z weryfikacją)”
Najnowsza i najnowocześniejsza modyfikacja popularnej rosyjskiej marki sprzętu. Jest na nim zainstalowane oprogramowanie w wersji finalnej, teraz możliwe jest wyświetlanie wykresów testowych w dynamice. W zestawie znajdują się wszystkie najpopularniejsze czujniki, sprzęt ma niewielkie gabaryty. Zalecany koszt dla sieci handlowych to 222 000 rubli.
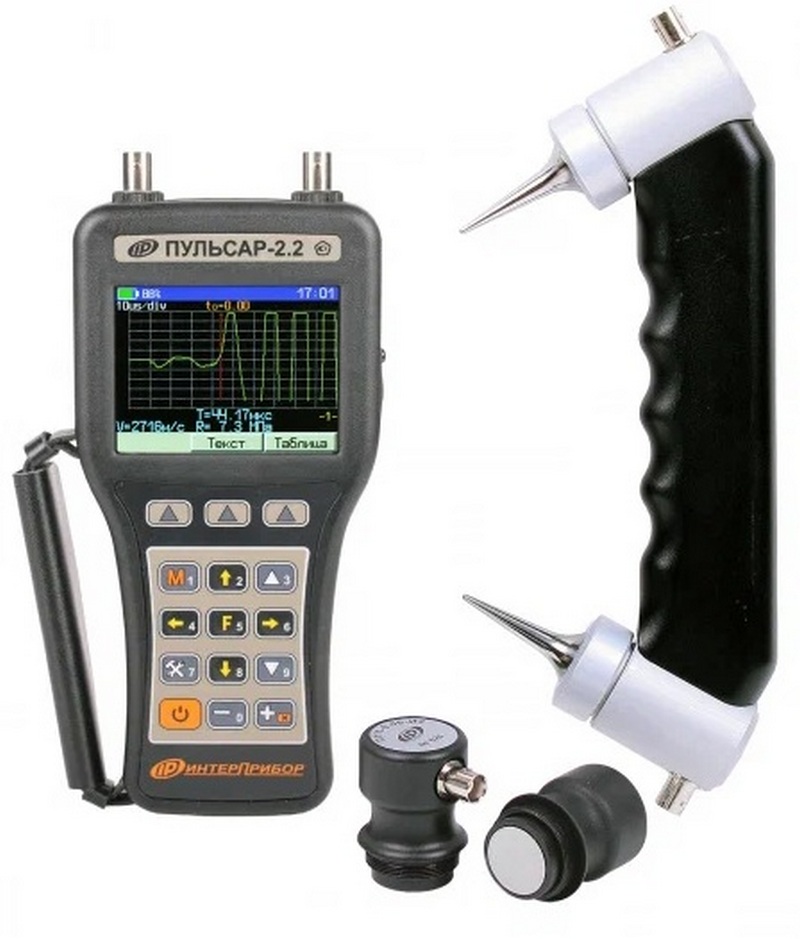
defektoskop Urządzenie ultradźwiękowe PULSAR-2.2 (z weryfikacją)
Zalety:
- Najnowsza wersja oprogramowania;
- Dobry sprzęt;
- Małe rozmiary.
Wady:
Wniosek
Zawsze warto pamiętać, że przedmiotowy sprzęt o wysokiej precyzji pod względem masy, wymiarów, rodzaju zasilania, metod wykrywania wad, odporności na wibracje musi spełniać wymagania normy państwowej nr 23049 z 1984 roku.Ponadto każdy model musi mieć określoną minimalną liczbę bloków roboczych, za pomocą których można wykonywać najbardziej standardowe operacje.