Wózek spawalniczy (lub ciągnik spawalniczy) to specjalny rodzaj samobieżnego sprzętu, który służy do ciągłego i dokładnego przesuwania palnika spawalniczego (lub kilku) wzdłuż wymaganej trajektorii podczas procesu spawania. Niewielki rozmiar tego mechanizmu pozwala na zastosowanie go w najbardziej niedostępnych pozycjach. Tego typu zmechanizowane urządzenie jest w stanie zgrzewać szwy o zwiększonej długości, eliminując jednocześnie czynnik błędu ludzkiego i zachowując wysoki stopień jakości wykonywanej pracy.
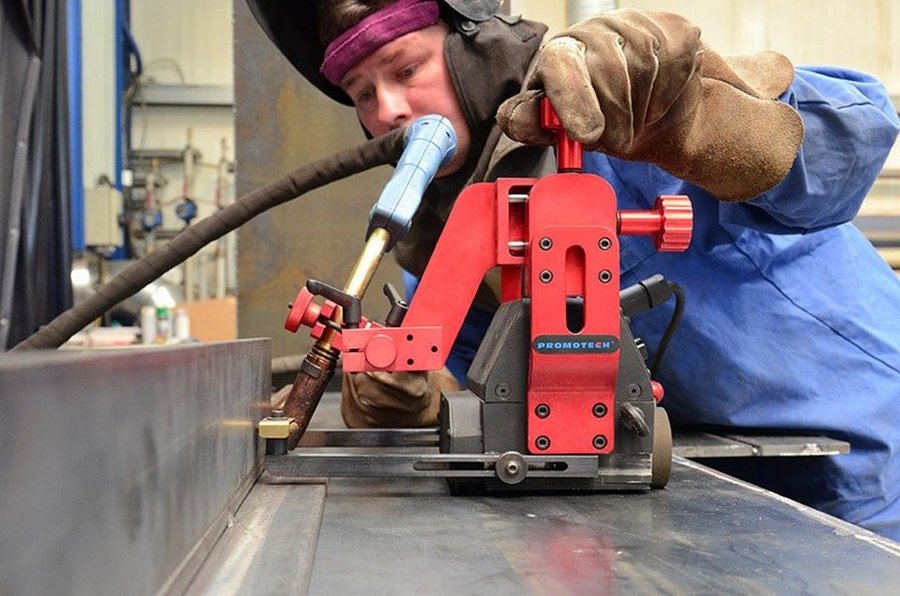
Podstawowe szczegóły projektu
Za pomocą wózka spawalniczego wykonuje się spawanie łukiem elektrycznym. Jak każda maszyna automatyczna, działa według określonego programu, ma specjalne kółka, którymi się porusza. Główną cechę tego urządzenia można nazwać jego samobieżnością - ruch odbywa się wzdłuż szyn (ułożonych wzdłuż osi szwu) niezależnie lub wektor ruchu jest określany przez osobę. Wózki są dość kompaktowe i bardzo łatwo je przetransportować między sąsiednimi pomieszczeniami ze względu na to, że szyny do przemieszczania są lekkie i można je przewozić razem z urządzeniem. Głównym elementem roboczym jest głowica spawalnicza, przez którą podawany jest gaz płynny. Dużą rolę odgrywają również materiały eksploatacyjne i topnik ochronny. Ogólnie konstrukcja urządzenia przypomina wózek z panelem sterowania, na którym znajduje się sam ciągnik i dodatkowe mechanizmy. Większość detali może być wbudowana w mechanizm lub wyjęta z jego konstrukcji. Same opisane urządzenia są najczęściej używane w przedsiębiorstwach przemysłowych oraz w warsztatach średniego szczebla. Mogą być używane zarówno osobno, jak i jako część dużego przenośnika.Ilość możliwej funkcjonalności wpłynie bezpośrednio na cenę bryczki (np. droższe modele mają możliwość automatycznej kontroli poprawności geometrii zastosowanego szwu lub mogą samodzielnie regulować ilość wydawanego topnika ochronnego).
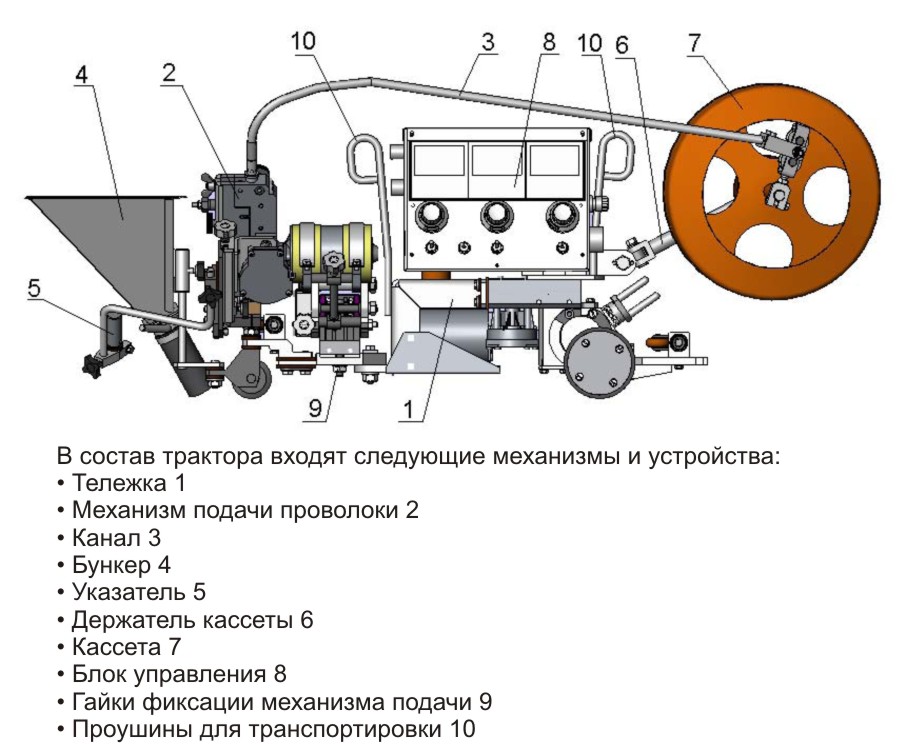
Istniejąca klasyfikacja
Do tej pory opracowano kilka rodzajów rozważanego sprzętu, które można pogrupować według określonych kryteriów. Jeśli mówimy o liczbie silników zainstalowanych w wózku spawalniczym / ciągniku, można je podzielić na:
- Jednosilnikowy - cały ruch odbywa się za pomocą jednego silnika (mają prostsze parametry techniczne, są jednak lekkie);
- Dwusilnikowy - ruch karetki jest kontrolowany przez dwa silniki wzdłuż różnych osi (takie urządzenie jest bardziej masywne, ale ma wyższy stopień niezawodności, a jego parametry można regulować na dokładniejszym poziomie).
Klasyfikacja według stosowanych metod ochrony może występować według następujących typów:
- „Spawanie łukiem otwartym” - przy tej metodzie nie stosuje się żadnej ochrony, dlatego szew może być poddawany różnym negatywnym wpływom, jednak sam proces produkcji staje się tańszy;
- „Z ochroną gazową” - dzięki tej metodzie, tworząc środowisko ochronne z aktywnych / obojętnych gazów, tlen nie może dostać się do szwu i nie jest poddawany innym negatywnym wpływom;
- „Łuk zanurzony” - w tej metodzie stosuje się dodatkowy topnik, który poprawia jakość szwu na spawanym metalu i jednocześnie chroni produkcję przed negatywnymi wpływami;
- „Zastosowanie elektrody nietopliwej” - materiał wypełniający po prostu nie jest używany w procesie spawania.
Klasyfikacja według metody jednocześnie podpartych łuków spawalniczych:
- Pojedynczy łuk - prowadzi jeden łuk, przystosowany do większości tradycyjnych operacji, jest najprostszą metodą i jest stosowany w wózkach jednosilnikowych;
- Dwułukowy - jest w stanie prowadzić parę łuków równolegle, podczas gdy spawanie odbywa się jednocześnie, co znacznie przyspiesza najbardziej skomplikowane operacje, np. w produkcji masowej;
- Trzyłukowy - zdolny do wprowadzenia trzech łuków jednocześnie i przeznaczony do profesjonalnych prac spawalniczych o dużej złożoności (może być stosowany tylko w układach dwusilnikowych).
Ciągnik spawalniczy z PU dla wszystkich pozycji
Ten typ ciągnika porusza się na elastycznych szynach stalowo-aluminiowych, które są mocowane do obrabianej konstrukcji za pomocą zacisków magnetycznych. Elastyczność szyny pozwala powtórzyć kontury spawanego przedmiotu, podczas gdy szew zostanie nałożony ściśle według określonego wzoru. Ta metoda automatyzacji jest niezwykle wydajna w tworzeniu ciągłych i długich szwów. Również jedną z najważniejszych cech tego typu ciągnika jest ich innowacyjna funkcja sterowania, dzięki której prędkość karetki jest utrzymywana niezależnie od otrzymanego ładunku (w granicach 45 kilogramów). Fakt ten oznacza, że ciągnik może podczas pracy podnosić podajniki drutu spawalniczego, a także kable potrzebne do pracy urządzenia.
W celu zwiększenia elastyczności zautomatyzowanego procesu opracowano kilka szablonów programów.Istnieją ciągniki, które pracują zgodnie z programem do wykonywania szwów spawalniczych w łańcuchu prostych operacji („Natychmiastowy start”, „Stop”, „Start łuku spawalniczego”, „Spawanie”, „Stop”, „Powtórz” ). W efekcie celem stosowania szablonów algorytmów jest zwiększenie szybkości i dokładności spawania, co znacznie przyspiesza proces produkcyjny w porównaniu z klasycznym spawaniem ręcznym. W ten sposób PU (kontrola oprogramowania) jest idealną opcją do realizacji projektów na dużą skalę, w których konieczne jest zautomatyzowanie tego samego rodzaju procesów.
Szczegółowe zalety funkcjonalne stosowania ciągników spawalniczych
Zastosowanie samojezdnych ciągników spawalniczych do półautomatycznego spawania w gazach osłonowych odgrywa istotną rolę w zakresie pełnej automatyzacji złożonych procesów produkcyjnych. Jakościowo zmieniają warunki, szybkość i dokładność pracy w porównaniu z konwencjonalnym spawaniem ręcznym, a wśród ich bezpośrednich zalet są:
- Zastosowanie standardowego sprzętu spawalniczego - w przypadku stałego użytkowania w branży traktorów spawalniczych nie ma już konieczności dokupowania innych opcji na urządzenia specjalne - większość traktorów jest łatwo kompatybilna z tradycyjnymi półautomatami spawalniczymi oraz szeroką gamą palniki spawalnicze.
- Nie ma potrzeby ponoszenia kosztów finansowych na dodatkowe szkolenie operatorów – obsługa samego wózka spawalniczego jest intuicyjna, a może z niego skorzystać każdy spawacz zaznajomiony z obsługą półautomatów. Jedyną rzeczą jest to, że nadal musisz przejść przez wstępną odprawę, ale może to zająć maksymalnie 2 dni.Ponadto spawanie karetek można powierzyć nawet specjalistom, którzy posiadają niższe kwalifikacje nawet w stosunku do procesu ręcznego. Wynika to z faktu, że główne parametry spawania (prędkość podawania drutu, napięcie i prąd) są ustawiane przez bardziej doświadczonych specjalistów bezpośrednio na panelu sterowania, a prędkość sterowania spawaniem (prędkość wózka) i nachylenie uchwytu spawalniczego w stosunku do obrabianej powierzchni są również poza kontrolą obecnego operatora i ustalane z wyprzedzeniem. Operator musi więc jedynie ustawić wózek w odpowiedniej pozycji nad spawanym przedmiotem, wybrać żądany tryb spawania i nacisnąć przycisk „Start”. Potem pozostaje tylko wizualnie kontrolować całą procedurę.
- Poprawa ogólnej jakości - podczas spawania ciągnikiem odległość od kąta nachylenia palnika (zarówno w poprzek, jak i wzdłuż spoin) do wyjścia dyszy palnika spawalniczego, która ustala wielkość łuku, będzie stała i kontrolowana przez spawacza latarka zainstalowana w uchwycie. Prędkość pozostanie niezmieniona na całej długości łuku wzdłuż złącza. Kontroli podlega również trajektoria ruchu łuku. Wszystko to przyczynia się do kontrolowanej penetracji, tworzenia drobno łuszczącej się i jednolitej struktury spoiny, zapobiegania powstawaniu podcieni, wzrostu jakości geometrycznej nałożonej spoiny oraz tworzenia płynnego płynięcia do metalu podstawowego osadzonego ściegu. Dzięki zastosowaniu bloku oscylacyjnego palnika poprawia się jakość zgrzewania licowania i wypełniania szwów przy wielu przejściach.Nawet jeśli złącze spawane nie jest prawidłowo zmontowane, dobrą jakość pracy można uzyskać dzięki temu, że większość wózków ma rolki zatrzymujące, które mogą śledzić linię złącza, jednocześnie korygując ścieżkę palnika spawalniczego.
- Zwiększenie intensywności procesu spawania – to naturalne, że każda automatyzacja dowolnego procesu umożliwia zwiększenie intensywności pracy. Jeśli chodzi o spawanie karetek, to według statystyk intensywność pracy wzrośnie o 40-45% całkowitego czasu pracy, co oznacza oszczędność około trzech lub trzech i pół godziny na zmianę w porównaniu ze spawaniem ręcznym. W przypadkach, w których używane są drogie i wielofunkcyjne traktory spawalnicze, liczba ta może zbliżyć się do oszczędności rzędu pięciu lub sześciu godzin pracy na zmianę. Jako prosty przykład można przytoczyć następującą sytuację: nawet doświadczony spawacz z pewną dozą wytrwałości rzadko będzie w stanie wykonać szew dłuższy niż metr bez zmiany pozycji. W każdym razie będzie musiał albo poruszać się wzdłuż wykonywanego szwu, albo zmieniać położenie przedmiotu obrabianego. Naturalnie, wykonując te operacje, spawacz zmuszony jest do wygaszenia łuku. Wznawiając pracę i przed obowiązkowym spawaniem zakładki szwu o 15-25 milimetrów, musi najpierw oczyścić koniec szwu z folii i rozprysków. Natomiast ciągnik spawalniczy porusza się bez przerwy, jednocześnie zgrzewając szew na dowolnej długości, dzięki czemu nie musi zmieniać pozycji (jak spawacz) podczas przerywania operacji. W ten sposób nie występują okresowe przerwy w pracach spawalniczych.Ponadto istotną rolę odegra również brak konieczności okresowego odpoczynku spawacza, ponieważ nie jest konieczne stałe kontrolowanie postępu prędkości spawania i jednoczesne utrzymywanie odpowiedniego zasięgu elektrody w celu uzyskania lepiej spawać. Pokazuje to, że operator może monitorować nie tylko własny mały odcinek łuku, ale jest również w stanie ogólnie kontrolować sytuację, w tym obserwować działania innych operatorów, którzy przetwarzają ten sam obiekt, aby w odpowiednim czasie koordynować z nimi swoje działania . To samo można powiedzieć o kontroli zachowania samej konstrukcji w procesie pracy. Dużym plusem może być zastosowanie urządzenia z dwoma palnikami spawalniczymi, które umożliwia jednoczesne wykonanie dwóch szwów równolegle lub wykonanie dwóch przejść wzdłuż tego samego szwu przy rozdzielaniu krawędzi. Jednocześnie jeden operator jest w stanie obsłużyć kilka wagonów jednocześnie, co jeszcze kilkakrotnie zwiększy wydajność.
- Zmniejszenie udziału procentowego w zakresie zgrzewania deformacyjnego – kontrola nad dopływem ciepła pozwala na zmniejszenie całkowitego procentu deformacji obrabianej konstrukcji po zakończeniu pracy. Ta okoliczność jest bezpośrednią konsekwencją faktu, że podczas obróbki zachowane są bardzo dokładne parametry spawania – napięcie łuku i prędkość spawania, których nie można osiągnąć w ramach produkcji ręcznej. Ponadto ciągłe gaszenie / zajarzenie łuku, gdy spawacz porusza się wzdłuż długości szwu, a także konieczność wykonywania procedury zamykania szwu - wszystko to wpływa na ryzyko kolejnych odkształceń. Należy zauważyć, że szycie dwoma wózkami jednocześnie zmniejszy ryzyko ewentualnych negatywnych konsekwencji o połowę.
- Oszczędności na materiałach spawalniczych – taka okoliczność powstaje dzięki wdrożeniu drobniejszych regulacji parametrów spawania i ich utrzymaniu przez cały czas pracy. Jako główny czynnik można wskazać zmniejszenie strat objętości drutu spawalniczego podczas rozprysków. Wpływa również na brak przerw podczas pracy, podczas poruszania się wzdłuż złącza spawacza, a właściwie na samo wznowienie pracy (brak konieczności nakładania się szwów znacznie oszczędza materiały spawalnicze). Liczbę przejść można zmniejszyć dzięki możliwości spawania z drganiami poprzecznymi. Ponadto, przy jednorodności i jednorodności wszystkich operacji, zmniejsza się zużycie gazu ochronnego, co będzie znaczącym artykułem pod względem oszczędności, gdy do ochrony stosuje się drogie mieszaniny gazowe na bazie argonu.
- Procesy pomocnicze będą wymagały mniejszych kosztów - koszt dodatkowych operacji, takich jak czyszczenie strefy wpływu ciepła i gratowanie szwów, a także usuwanie wzmocnienia szwów, zostanie znacznie zmniejszony ze względu na to, że już teraz uzyska się gładkie i schludne szwy w pierwszym przejściu. Zmniejszenie poziomu odprysków wpłynie również na koszty związane z fugowaniem.
- Zwiększenie ekologicznego poziomu produkcji – przyjazne dla środowiska warunki pracy zostaną osiągnięte dzięki temu, że spawacz będzie znajdował się na miejscu operatora, a nie siedzieć w bezpośredniej bliskości dymu i ciepła, które powstają podczas spawania łukowego.
Dzięki temu za pomocą spawania ciągnikowego można zautomatyzować każde, nawet małe przedsiębiorstwo i doprowadzić je do „plusa”.Dotyczy to zwłaszcza tych firm, w których kadra specjalistów ma wystarczające doświadczenie w pracy z półautomatycznym spawaniem w gazach osłonowych – wtedy wynik zostanie osiągnięty w możliwie najkrótszym czasie i będzie bardziej wyraźny. Ponadto wprowadzenie powozów/ciągników nie będzie wymagało ekstremalnie dużych inwestycji i zwróci się dość szybko (chyba że planowany jest super duży i skomplikowany projekt) i jest czas na montaż:
- Niektóre modele wózków kosztują nawet mniej niż ich odpowiedniki w zanurzonych ciągnikach;
- Pomimo tego, że wolumeny zakupów materiałów eksploatacyjnych (gazów osłonowych i drutu eksploatacyjnego) pozostaną na tym samym poziomie, ich koszty znacznie spadną;
- Nie ma potrzeby kupowania dodatkowego sprzętu do kalcynacji topnika, a także ponownego wyposażenia do tego specjalnego pomieszczenia;
- Nie ma potrzeby radykalnej zmiany technologii realizowanych procesów (np. nie ma potrzeby wprowadzania nowych rodzajów cięcia krawędzi);
- Nie ma potrzeby szkolenia personelu odpowiednio w zakresie nowych metod spawania, nie będzie potrzeby dodatkowej certyfikacji i atestacji pracowników.
Istniejące braki
Niestety, przy wszystkich istotnych pozytywnych aspektach, rozważane urządzenia mają również istotne wady:
- Przed rozpoczęciem pracy musisz bardzo dokładnie wprowadzić wszystkie ustawienia;
- Precyzyjny sprzęt podlega złożonym awariom, dlatego szybkie naprawy i wznowienie pracy są niezwykle wątpliwe;
- Istnieją określone ograniczenia dotyczące maksymalnej/minimalnej średnicy szwów pętelkowych;
- Sama technika najczęściej ma niewielką masę, ale przypadkowe nadmierne obciążenie może ją szybko wyłączyć;
- Obsługa wymaga pewnych umiejętności, co sprawia, że technika ta jest słabo dostępna dla małych firm;
- Wysoka cena.
Problemy właściwego wyboru
Każde zadanie spawalnicze ma swoje specyficzne parametry, które należy dokładnie sprawdzić przy zakupie wózka/ciągnika. W przypadku zadań o małych objętościach, które nie wymagają szczególnej złożoności i wymagają jedynie ciągłego wykonywania tego samego rodzaju operacji, odpowiednie są maszyny jednosilnikowe bez sterowania programowego. Są łatwe w obsłudze, nie stanowią szczególnej trudności w przypadku napraw. W przypadku, gdy wymagany jest projekt na dużą skalę, a tym bardziej jego realizacja w krótkim czasie, lepiej kupić próbki wielołukowe i wielosilnikowe. To samo będzie dotyczyło wdrażania produkcji masowej.
WAŻNY! Przy zakupie głównym kryterium wyboru powinien być wskaźnik maksymalnego i minimalnego prądu, a także rozmiar użytych przewodów eksploatacyjnych!
Ocena najlepszych ciągników i wózków spawalniczych na rok 2025
Segment cen budżetowych
II miejsce: „EvoSAW 1250-II”
To samobieżne urządzenie jest przystosowane do samodzielnego wykonywania prac spawalniczych przy użyciu topnika; podzielony konstrukcyjnie na dwa bloki (właściwie zautomatyzowane urządzenie i zasilanie falownika). Charakteryzuje się zwiększoną szybkością pracy - w ciągu sześćdziesięciu sekund z łatwością wykona szew o długości od 10 do 15 centymetrów. Jednak na szybkość zadań będzie miała wpływ grubość obrabianego metalu. Falownik może być używany między innymi jako samodzielne urządzenie do cięcia na zadaną głębokość (żłobienie łukiem powietrznym) lub jako spawarka ręczna. Opakowanie zawiera system ochrony przed zwarciem i przegrzaniem.Krajem pochodzenia jest Rosja, sugerowana cena detaliczna to 250 000 rubli.
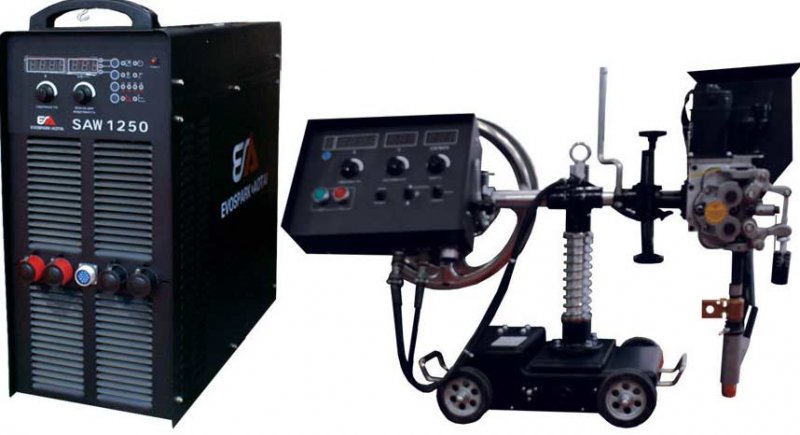
EvoSAW 1250-II
Zalety:
- Obecność ochrony;
- Możliwość osobnego wykorzystania elementów;
- Jakość wykonania.
Wady:
- Ma ograniczenia grubości spawanego metalu.
I miejsce: ADF-1000
Ta próbka rosyjskiego producenta może wykonywać wielowarstwowe i jednowarstwowe spawanie z napawaniem drutu spawalniczego pod osłoną topnika. Będzie to jednak wymagało trójfazowego połączenia elektrycznego. Oprogramowanie dołączone do zestawu rozwiązuje problem synchronizacji prędkości ruchu i podawania drutu elektrodowego. Urządzenie jest w stanie poruszać się zarówno po wstępnie zainstalowanych szynach, jak i bezpośrednio po powierzchni obrabianego obiektu. Dostępny jest pilot zdalnego sterowania, za pomocą którego można również regulować napięcie spawania. Element roboczy - głowica - jest ruchomy, może być montowany pod określonym kątem do powierzchni roboczej. Dla wygody kontroli wizualnej w projekcie przewidziano oznaczenie laserowe. Szwy można nakładać zarówno w technice pierścieniowej, jak i prostej. Urządzenie umożliwia spawanie bez krawędzi tnących lub z nimi (doczołowo), łączenie w „taurus” (pod kątem) i nakładanie szwów. Zalecana cena to 260 000 rubli.
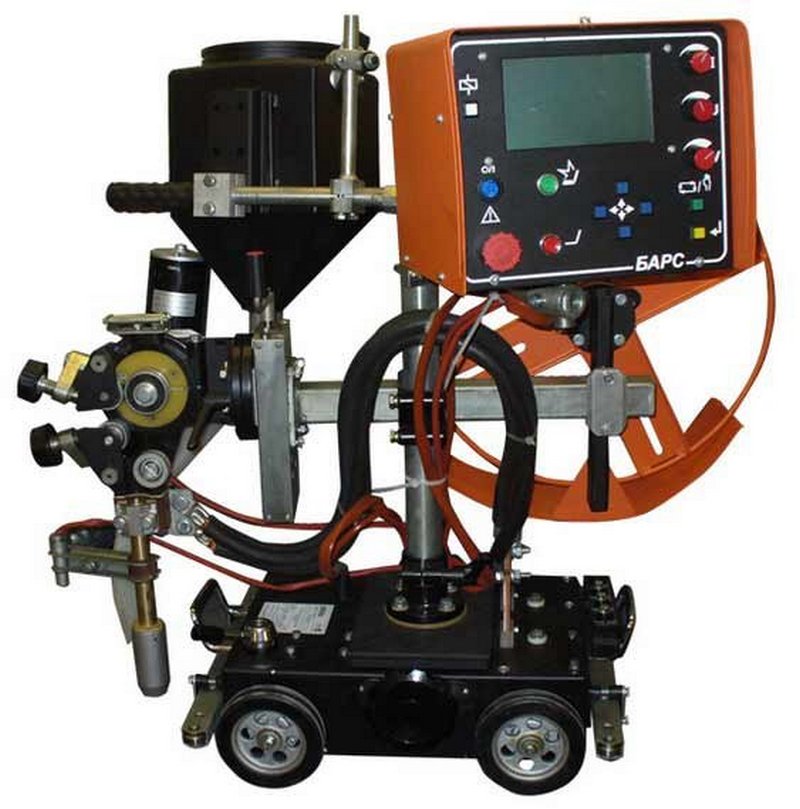
ADF-1000
Zalety:
- Możliwy jest ruch na powierzchni obiektu roboczego;
- Obecność znacznika laserowego;
- Posiada pilota.
Wady:
- Wymagane jest trójfazowe podłączenie do sieci.
Średni segment cenowy
II miejsce: Promotech JASZCZURKA
Ten przykład ma stabilną prędkość poruszania się, która pozostaje niezmienna przez cały przepływ pracy.Fakt ten pozwala osiągnąć niezwykłą precyzję nakładania spoiny, a także zapewnić jej lepszą jakość. Jednocześnie materiał wypełniający będzie wykorzystywany niezwykle ekonomicznie. Maszynę można zaprogramować do szycia długim lub specjalnym ściegiem za pomocą ściegów. Tylko przez naciśnięcie dwóch przycisków można określić rodzaj żądanego szwu, a parametry długości, odstępu między wierszami, wypełnienia szwu, czasu wypełnienia krateru można już wstępnie ustawić. Bardzo ważną opcją jest obecność jednostki oscylacyjnej, za pomocą której automatycznie wybierane są niezbędne kryteria operacji spawania. Blok ten znacznie rozszerza możliwości urządzenia, co jest szczególnie ważne w przypadku szwów pionowych oraz szwów z cięciem wzdłuż krawędzi. Zalecana cena to 312 000 rubli.
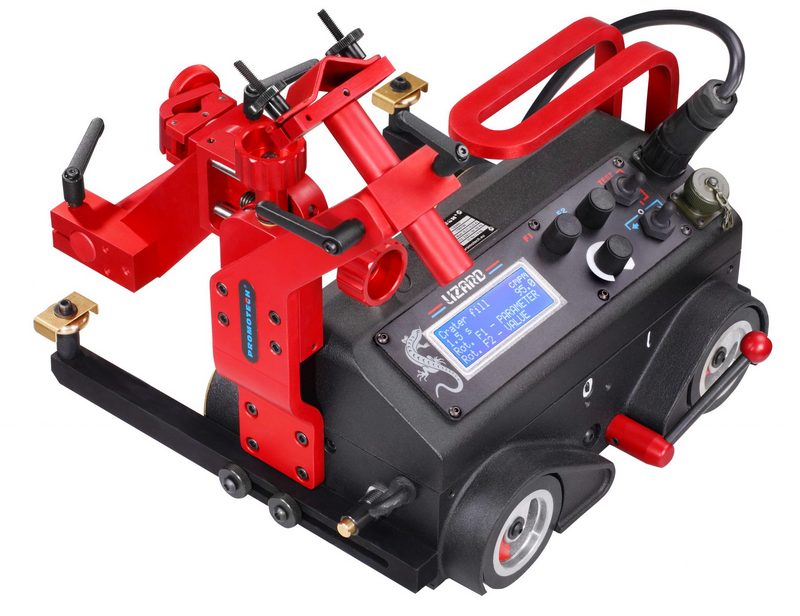
Promotech JASZCZURKA
Zalety:
- sztywny i lekki jednoczęściowy korpus;
- Obecność magnetycznego systemu pozycjonowania;
- Możliwość nagrywania do 40 szablonów programów.
Wady:
I miejsce: „Riland-Aurora PRO MZ 1250”
Dobra próbka chińskiego producenta, który ma architekturę modułową z osobnym falownikiem. Urządzenie może wykonywać operacje spawania łukiem krytym w trybie automatycznym. Ten tryb wpłynie pozytywnie na ogólne przyspieszenie produkcji, a jakość zastosowanych szwów nie zostanie utracona. Potrafi spawać pod kątem, a także nakładać się na siebie, a nawet doczołowo. Może poruszać się zarówno po obrabianym obiekcie, jak i po danym wektorze za pomocą zainstalowanych szyn. Pozycja spawu jest dość regulowana - może być umieszczona zarówno na zewnątrz toru, jak i wewnątrz niego.Samo urządzenie jest bardzo proste konstrukcyjnie, co oznacza zwiększoną niezawodność. Ochrona przed przepięciami i nagrzewaniem - obecna. Zapewnione jest wysokiej jakości wymuszone chłodzenie, co wpływa na wydłużenie żywotności. Zalecana cena to 338 000 rubli.
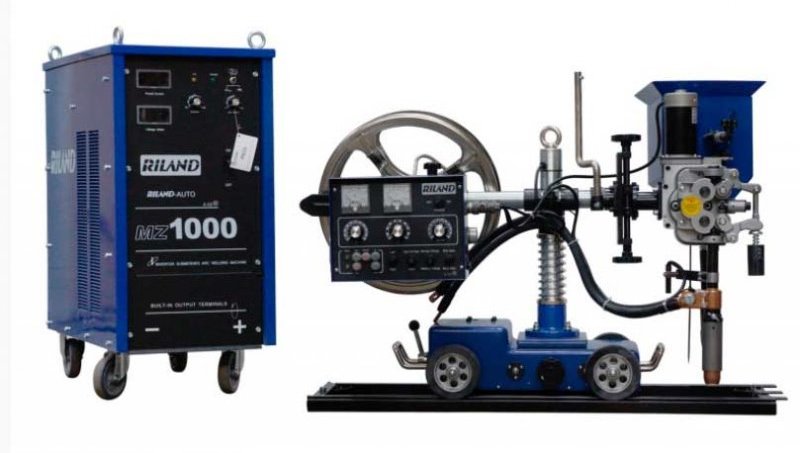
Riland-Aurora PRO MZ 1250
Zalety:
- Dostępny system wymuszonego chłodzenia;
- Potrafi wykonywać spawanie w nietypowy sposób;
- Oddzielna architektura modułowa.
Wady:
Klasa premium
2 miejsce: „Svarog MZ1000”
Kolejna rosyjska próbka przeznaczona do pracy z metalowymi przedmiotami o grubości od 4 do 30 milimetrów. Wykazuje wysoką wydajność podczas używania urządzenia w niemal ciągłych operacjach produkcyjnych. Równość łuku zapewnia precyzyjna regulacja ustawianych parametrów prądu, co oznacza lepsze szycie. Jednostka ma wewnętrzny obwód stabilizujący, który kontroluje wahania napięcia wejściowego, ale do jego podłączenia będzie potrzebna sieć trójfazowa. Wygodne zarządzanie i obsługę zapewniają jasne i kontrastowe wyświetlacze informacyjne oraz panel sterowania. Do pamięci można wczytać do 100 szablonów algorytmów, co pozwoli Ci nie konfigurować sprzętu za każdym razem. Sugerowana cena to 350 000 rubli.
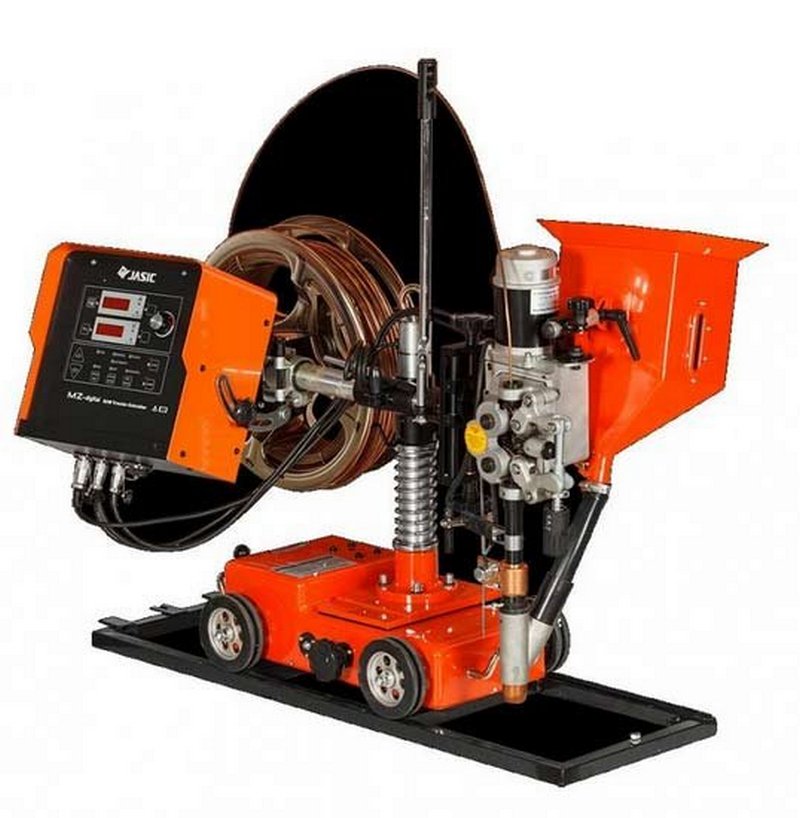
Svarog MZ1000
Zalety:
- Do 100 programowalnych wzorów;
- Istnieje wewnętrzny obwód stabilizacji;
- Wysokiej jakości szwy.
Wady:
- Wymagana jest sieć trójfazowa.
1. miejsce: ESAB A2 Multitrac
Znakomity, ale bardzo drogi model europejskiego producenta. W procesie produkcyjnym może pracować dwoma łukami, rozszczepiając drut eksploatacyjny.Dostęp powietrza do obszaru zastosowania szwu jest uniemożliwiony przez dostarczanie gazów obojętnych. Po zainstalowaniu specjalnego adaptera możliwe jest wykonanie żłobienia powietrznego elektrodą węglową. Falownik tyrystorowy może zapewnić stabilny łuk nawet przy niskim napięciu. Zalecana cena to 1 100 000 rubli.
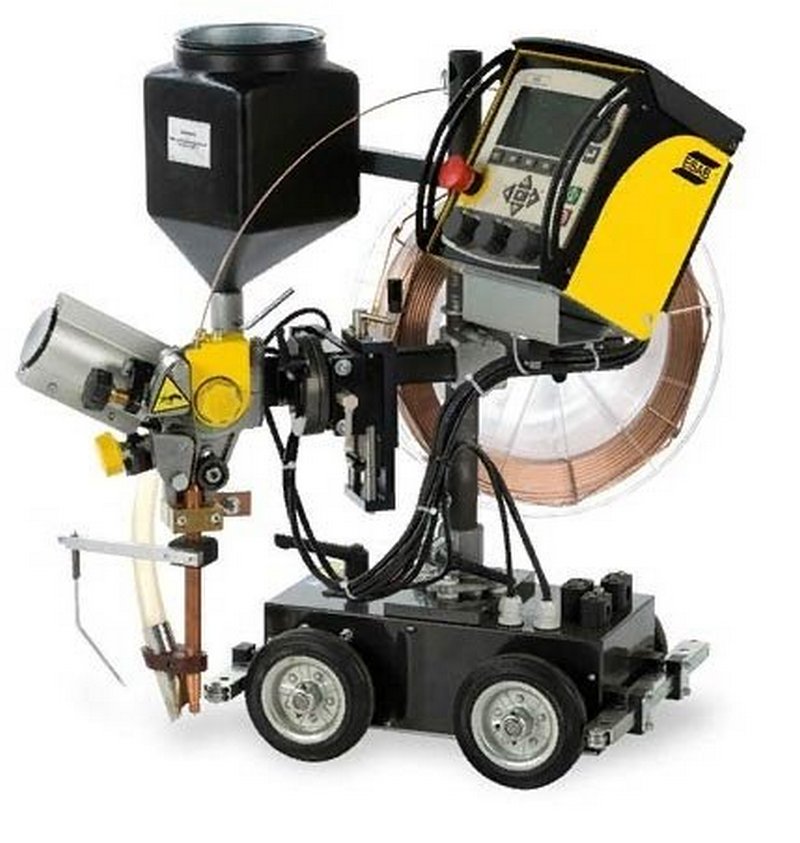
ESAB A2 Multitrac
Zalety:
- Stabilność łuku przy niskim napięciu;
- Praca równoległa z dwoma łukami;
- falownik tyrystorowy.
Wady:
Zamiast epilogu
Ciągniki/wózki spawalnicze to proste, ale funkcjonalne rozwiązanie do automatycznego spawania łukowego. Są w stanie poruszać się po wcześniej wybranej ścieżce lub po specjalnych szynach, co pozostawia na osobie jedynie obowiązek wizualnej kontroli wykonywanej pracy. Głównym zadaniem operatora jest prawidłowe i odpowiednie ustawienie niezbędnych ustawień zgodnie z wykonywanym zadaniem. Maszyna może wykonać wszystkie prace samodzielnie. Rodzaj pracy może być zupełnie inny, więc same urządzenia mogą być lekkie i niedrogie lub nieporęczne i drogie. Niemniej jednak bardziej słuszne jest stwierdzenie, że ciągnik lub wózek spawalniczy koncentruje się przede wszystkim na produkcji przemysłowej.