Ein Ultraschallprüfgerät ist ein Gerät, das dafür ausgelegt ist, Fehler in einem Objekt zu erkennen, ohne seine Integrität zu beschädigen. Verformungen werden durch das Auftreffen von Ultraschallwellen auf das Objekt erkannt. Die Ausrüstung ist sehr gefragt, da ihre Funktionsweise die einzige ist, die es Ihnen ermöglicht, die genauesten Diagnoseergebnisse zu liefern, ohne das Forschungsobjekt zu zerlegen.
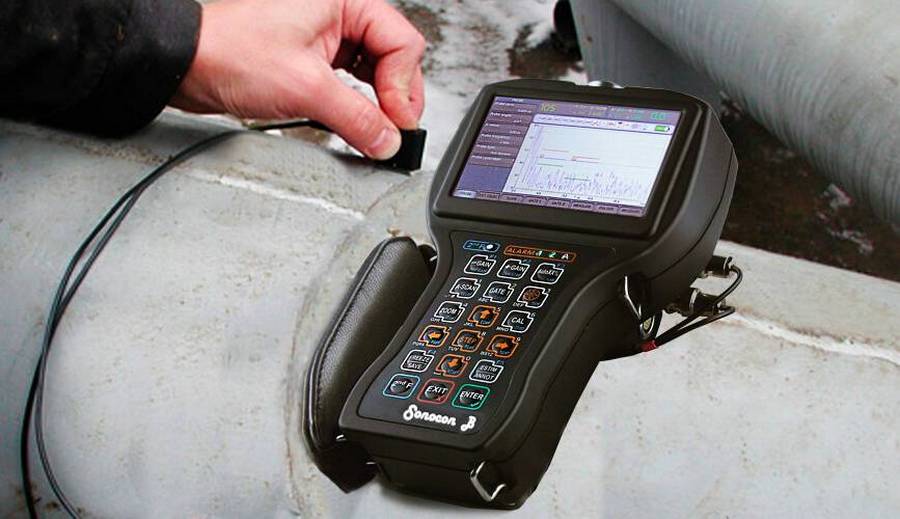
Ultraschallprüfgerät: allgemeine Informationen
Ultraschall durchdringt eine Schicht aus massivem Eisen und kann das Vorhandensein kleinster Risse erkennen, die sich möglicherweise im Inneren des Objekts befinden. Das Gerät wird in der Lage sein, einen Defekt in einer Tiefe von 5 bis 50 Millimetern mit hoher Genauigkeit zu erkennen. Die betrachteten Geräte können unterschiedliche Empfindlichkeitsstufen aufweisen. Dieser Indikator hängt von der Größe und den Abmessungen des erkannten Fehlers ab. Der Anwendungsbereich des Geräts ist sehr breit, aber meistens werden sie verwendet, um die Qualität von Metallen in der Produktion zu bestimmen.Die Geräte verfügen über eine intuitive Bedienung, bieten eine einheitliche und effiziente Nutzung und zeichnen sich durch eine erhöhte Genauigkeit aus, die es Ihnen ermöglicht, qualitativ hochwertige Ergebnisse zu erzielen und verschiedene Produktionsfehler rechtzeitig zu erkennen und zu beheben.
Prinzip der Ultraschallsteuerung
Der betreffende Gerätetyp wird normalerweise verwendet, um das Festigkeitsniveau an Schweißnähten zu kontrollieren. In diesem Fall arbeitet das Gerät während des Betriebs wie folgt: Es werden bestimmte Schallwellen in die Bleche geleitet, die das Gehäuse in Schwingungen versetzen. Sie können von den folgenden Arten sein:
- Hyperschall;
- Ultraschall;
- Standardton;
- Infraschall.
Während des Durchgangs des Ultraschalls bildet der Raum, durch den er sich ausbreitet, gleichmäßige Schwingungen in Bezug auf seinen Ruhepunkt aus. Bei Feststoffen können Quer-/Längsschwingungen auftreten, wodurch Sie die Qualität der Schweißnähte mit höchster Genauigkeit kontrollieren können. Die Ausbreitungs- und Versorgungsgeschwindigkeit der beschriebenen Wellen ist direkt abhängig von der Stärke / internen Umgebung des untersuchten Objekts. Die Intensität der Wellen kann eingestellt werden. Während sich die Welle ausbreitet, lässt ihre Stärke allmählich nach. Basierend auf der Steuerung der Extinktionsrate wird es möglich sein, die Stärke der Naht zu beurteilen. Das Gerät hingegen zeigt den Schwächungskoeffizienten des Ultraschalls an und erstellt ihn basierend auf dem Grad der Absorption und Streuung. Die Endgenauigkeit ist sehr hoch, sodass Sie sich konkrete Vorstellungen über die Qualität des Metalls, die Stärke der Naht und das Fehlen / Vorhandensein anderer Fehler machen können.
Beliebte Arten der modernen Produktionsfehlererkennung
Zu den äußerst beliebten Instrumenten zur zerstörungsfreien Fehlersuche gehören: Wirbelstrom, akustisch (Ultraschall) und magnetisch. Es gibt andere Arten, aber ihre Verwendung ist nicht so weit verbreitet, da das Prinzip ihrer Arbeit etwas kompliziert ist.
Ultraschall (akustisches Format)
Ein akustischer Fehlerdetektor wird allgemein als eine Reihe von zerstörungsfreien Prüfgeräten verstanden, die in ihrer Funktionalität ähnlich sind. Ihre Wirkung basiert auf den Prinzipien akustischer Wellen. Nach einfachsten physikalischen Prinzipien können die Grundindikatoren einer Schallwelle bei der Ausbreitung in einer homogenen Mikroumgebung nicht verändert werden. Blockiert jedoch ein neues Medium den Weg der Welle, ändern sich Länge und Frequenz. Je höher die Schallfrequenz, desto genauer ist das Ergebnis, daher wird unter dem gesamten verfügbaren Bereich Ultraschall verwendet. Das Ultraschallgerät sendet Wellen aus, die das Prüfobjekt durchdringen. Wenn es Hohlräume oder Einschlüsse anderer Materialien sowie andere Defekte gibt, wird die Welle diese ausnahmslos erkennen und dies durch eine Änderung ihrer Parameter anzeigen.
Fehlerdetektoren, die nach dem Prinzip der Echoortung arbeiten, gelten als die zugänglichsten und am weitesten verbreiteten. Die Welle tritt in das Objekt ein und wird, wenn keine Fehler gefunden werden, nicht reflektiert bzw. das Gerät erhält keine Rückmeldung und es werden keine Verletzungen registriert. Wenn die Welle zurückkehrt, weist dies auf das Vorhandensein von Fehlern hin. In jedem Fall ist das Gerät selbst sowohl ein Generator als auch ein Ultraschallempfänger, was die Fehlersuche erheblich erleichtert. Die Wirkungsweise des Spiegels ähnelt der Echoortung, verwendet jedoch separate Geräte - dies ist ein Generator und ein Empfänger.Der Vorteil dieser Methode liegt darin, dass sich beide Geräte auf der gleichen Seite des Untersuchungsobjekts befinden, was das Einrichten, Justieren und Messen qualitativ vereinfacht. Unabhängig davon sind die Methoden der Ultraschallanalyse zu erwähnen. Hier wird der Begriff „Schallschatten“ verwendet. Wenn sich im Inneren des Objekts ein Defekt befindet, trägt dieser zur sofortigen Dämpfung von Vibrationen bei und erzeugt so einen „Schatten“. Dieses Prinzip basiert auf dem Schattenverfahren der Fehlersuche mittels Ultraschall, bei dem sich Empfänger und Sender auf der gleichen Schallachse, aber auf gegenüberliegenden Seiten befinden. Die Nachteile eines solchen Geräts bestehen darin, dass für seinen vollwertigen Betrieb strenge Bedingungen für die Abmessungen, die Konfiguration und den Rauheitsgrad des zu messenden Objekts erfüllt werden müssen, was auf eine schlechte Vereinheitlichung der Ausrüstung hinweist.
Wirbelströme und Magnetfelder (Wirbelstromformat)
Wirbelströmungen werden in Leitern erzeugt, wenn sie sich in unmittelbarer Nähe eines magnetischen Wechselfeldes bilden, basierend auf der Tatsache, dass diese Strömungen bei Vorhandensein von Defekten ihr eigenes Sekundärfeld reproduzieren und Wirbelstrom-Fehlererkennungsvorrichtungen arbeiten. Dadurch bildet die beschriebene Vorrichtung eines solchen Funktionsprinzips ein Primärfeld, und durch elektromagnetische Induktion entsteht ein Sekundärfeld, das die Möglichkeit bietet, Mängel des Forschungsgegenstandes zu erkennen und zu identifizieren. Das Gerät hingegen empfängt ein sekundäres Feld, registriert dessen Indikatoren und gibt ein Ergebnis über Art und Qualität des Fehlers aus.
Solche Geräte haben eine sehr hohe Leistung und der Überprüfungsprozess nimmt nicht viel Zeit in Anspruch.Wirbelströmungen treten jedoch nur in solchen Medien auf, die eine Leitfähigkeit besitzen, was auf die enge Spezialisierung dieser Apparatur hinweist.
Magnetisches Partikelformat
Dies ist eine weitere der häufigsten Methoden. Es wird zur Bewertung von Schweißnähten, zur Überprüfung der Festigkeit von Schutzschichten, der Zuverlässigkeit von Rohrleitungen usw. verwendet. Diese Methode ist besonders wertvoll für die Diagnose von Objekten mit komplexer geometrischer Form und schwer zugänglichen Stellen zur Überprüfung.
Das Funktionsprinzip dieses Verfahrens basiert auf den physikalischen Parametern magnetisierter Metalle. Mittels Permanentmagneten (oder deren Analoga), die ein kreisförmiges/längsmagnetisches Feld bilden können, wird ein spezielles Reagenz, ein magnetisches Pulver, auf das Testobjekt aufgebracht (Nass-/Trockenmethode). Unter dem Einfluss des Feldes wird das Pulver zu sogenannten Ketten verbunden, strukturiert und bildet ein deutliches Muster in Form von Wellenlinien auf der Oberfläche. Das resultierende Bild zeigt deutlich den Betrieb des Feldes, und wenn Sie die erforderlichen Parameter der gekrümmten Linien kennen, können Sie sehen, wo es Abweichungen gibt, und den Ort des Fehlers bestimmen. An der Fehlerstelle (Lunker, Risse) sammelt sich meist besonders viel Pulver an. Das Endergebnis wird festgelegt, indem das resultierende Bild mit einem Qualitätsstandard verglichen wird.
Andere Arten der Fehlererkennung
Fast jedes Jahr erscheinen ständig neue Techniken. Gleichzeitig verlieren die alten sofort ihre frühere Popularität. Viele moderne Geräte sind hochspezialisiert und werden nur für bestimmte Branchen eingesetzt.
Beispielsweise arbeiten Fluxgate-Geräte, indem sie die Impulse analysieren, die erzeugt werden, wenn sie sich entlang des Objekts bewegen.Sie werden bei der Herstellung von gewalzten Metallprodukten, in der allgemeinen Metallurgie und bei der Prüfung von Schweißnähten eingesetzt.
In Betrieb befindliche Bestrahlungsgeräte bestrahlen Objekte mit Alpha-, Beta-, Gamma- und Röntgenstrahlen und beschießen sie mit Neutronen. Das Ergebnis ist ein sehr detailliertes Bild des Objekts mit sichtbaren Inhomogenitäten und Defekten. Das Verfahren zeichnet sich durch hohe Kosten aus, die durch erhöhten Informationsgehalt kompensiert werden.
Kapillarmodelle wurden entwickelt, um externe Risse und Lücken zu erkennen, wenn sie einem speziellen Entwicklungsmittel ausgesetzt werden. Das Ergebnis wird rein visuell ausgewertet. Das Kapillarverfahren wird im Schiffbau, in der Luftfahrt und im Maschinenbau eingesetzt.
In der Energiewirtschaft werden alle Fehler in Produkten (die unter Hochspannung stehen) durch elektronenoptische Fehlerprüfgeräte erkannt. Sie können die kleinsten Änderungen von Oberflächenpartikel- und Koronaentladungen erfassen, was es ermöglicht, den Betrieb eines Objekts aus der Ferne zu analysieren, ohne seinen Betrieb zu unterbrechen.
Diagnostik vorbereiten
Vor Beginn der Prüfung ist es notwendig, die Oberfläche von Korrosionsspuren, Lackmaterialien und anderen Beschichtungen zu reinigen. Es ist jedoch nicht erforderlich, die gesamte Oberfläche zu reinigen, es reicht aus, einen Abstand von 70 Zentimetern einzuhalten. In dieser Form wird das Objekt für die Diagnostik vorbereitet, dennoch wäre es wünschenswert, zusätzlich die Durchgängigkeit der Ultraschallwelle zu überprüfen. Dazu können Sie Öl, Fett, Glycerin und andere flüssige Substanzen mit Fettgehalt verwenden. Als Nächstes müssen Sie das Scangerät für bestimmte Optionen anpassen und kalibrieren. Die Hauptaufgaben sind:
- Prüfung von Objekten mit einer Dicke von weniger als 20 Millimetern (es ist erlaubt, die Werkseinstellungen zu verwenden);
- Untersuchung von Objekten mit einer Dicke von mehr als 20 Millimetern (die Daten des ART-Diagramms werden den Einstellungen hinzugefügt);
- Diagnose der Zuverlässigkeit von Schweißnähten (komplexe Kalibrierung mit ART-Diagrammdaten und Klärung anderer komplexer Impulse erforderlich).
Erst nachdem die Konfiguration abgeschlossen ist, sollten Sie mit den Überprüfungsvorgängen fortfahren.
Erreichen des höchsten Niveaus an Forschungsgenauigkeit
Um eine maximale Genauigkeit des Ergebnisses zu erhalten, muss die Sonde des Geräts im Zickzack über die Oberfläche bewegt werden, während die Sonde um etwa 10-15% um die Achse gedreht werden muss. Wenn das Gerät beginnt, atypische Vibrationen zu erzeugen, muss an der erkannten Stelle die Sonde so weit wie möglich ausgedehnt werden, um den Ort der schlecht hergestellten Verbindung genauer zu bestimmen. Die Suche muss so lange durchgeführt werden, bis der Punkt bekannt ist, an dem die Wellenspitze am höchsten sein wird. Gleichzeitig muss berücksichtigt werden, dass das Gerät das Ergebnis mit einem gewissen Fehler zurückgeben kann, was eine Folge der Wellenreflexion von den Nähten ist. Dann sollten andere diagnostische Methoden angewendet werden. Wenn mehrere verschiedene Methoden zu einem einzigen Ergebnis führen, können Sie den Fehler beheben, indem Sie seine Koordinaten aufschreiben. Hersteller von Fehlerprüfgeräten stützen sich auf die Anforderungen der Landesnormen und empfehlen, ein Objekt mit mindestens zwei verschiedenen Verfahren zu prüfen. Alle erhaltenen Daten müssen in einem speziellen Journal oder einer Tabelle aufgezeichnet werden. So können Sie den Mangel am Objekt schnell beseitigen und die abschließende Diagnose beschleunigen, denn alle identifizierten Problemstellen sind bereits bekannt.
Fehler, die von Ultraschallprüfgeräten mit der höchsten Wahrscheinlichkeit erkannt werden
Die Kontrolle von Schweißnähten, die mit Geräten der betreffenden Art durchgeführt wird, ermöglicht Ihnen, sich ein klares Bild von der Situation zu machen.Ein richtig durchgeführtes Verfahren kann eine fast 100%ige Genauigkeit des Ergebnisses garantieren. Es gibt jedoch Nachteile, die ziemlich schwer zu erkennen sind. Aber es gibt viele erkannte 100-%-Fehler, und dazu gehören:
- Chips, Risse;
- Poren;
- Schweißnähte zu wenig gekocht;
- Laminieren von Metalllegierungen;
- Fisteln;
- Durchhängende Nähte am Anfang / Ende der gesamten Struktur;
- Korrosionsspuren;
- Gegenseitiger Ausschluss in einem Gelenk zweier verschiedener Metalle;
- Abweichung von geometrischen Indikatoren im Designschema.
Die Forschung an solchen Arten von Metallen wie:
- Stahl,
- Kupfer,
- Gusseisen.
Außerdem stehen die folgenden Arten von Nähten für die Ultraschalldiagnostik zur Verfügung:
- T-förmig;
- eben;
- quer;
- Längs;
- Ring.
Vorteile von Ultraschallprüfgeräten
Dazu können gehören:
- Erhöhte Genauigkeit und beschleunigte Erfassung von Bewertungsinformationen;
- Die geringen Kosten des Verfahrens selbst;
- Tragbarkeit der verwendeten Ausrüstung, die die Arbeit „im Feld“ ermöglicht;
- Die Möglichkeit, Forschungen durchzuführen, ohne den Betrieb des diagnostizierten Objekts zu unterbrechen;
- Keine Gefahr für Schweißnähte, Rohrhohlräume und andere feste Untergründe.
Schwierigkeiten bei der Auswahl
Die wichtigsten Parameter, die vor dem Kauf genau beachtet werden müssen, können genannt werden:
- Messbereich;
- Zweck und Zweck;
- Gesamtleistung;
- Komplexität der Montage/Konfiguration;
- Grenzen der Betriebstemperaturen;
- Verlässlichkeit.
Verschiedene Modelle haben unterschiedliche Messbereiche, was bedeutet, dass einige Geräte Fehler bis zu einem Mikrometer erkennen können, während andere auf zehn Millimeter begrenzt sind. Solche Details spielen zum Beispiel im Maschinenbau eine sehr wichtige Rolle, aber für Konstruktionszwecke ist eine hohe Genauigkeit nicht erforderlich.Daher macht es für letztere Industrie keinen Sinn, ein genaues und teures Gerät zu erwerben. Außerdem muss der Hersteller in den Begleitdokumenten angeben, für welche Art von Materialien ein bestimmtes Modell bestimmt ist und welche Mängel es aufweisen kann. Getrennt davon können besondere Anforderungen an die Beschaffenheit der Oberfläche, das Vorhandensein / Fehlen von Schutzschichten, die Form und die Abmessungen des Prüfgegenstands gestellt werden.
Die Leistungskennzahl bestimmt die Geschwindigkeit des Scannens und den Gegenstand des Vorgangs, der an eine bestimmte Zeiteinheit "angehängt" werden kann. Fluxgate- und Wirbelstrommodelle können also eine höhere Geschwindigkeit bieten, aber der Prozess der Magnetisierung und Arbeit mit jedem Abschnitt separat kann ziemlich lange dauern. Unabhängig davon ist der Installations- / Montage- / Konfigurationsprozess zu erwähnen. Handgehaltene tragbare Geräte, die leicht in eine Tasche passen, sind die beste Lösung für den diensthabenden Inspektionsdienst. Präzisere und komplexere Geräte erfordern immer zusätzliche Installations-/Einstellzeit. Da zerstörungsfreie Prüfungen sowohl im Innen- als auch im Außenbereich (auch in der kalten Jahreszeit) durchgeführt werden können, ist es notwendig, die Grenzen der Betriebstemperaturen festzulegen. Gleichzeitig müssen Sie sich um die Möglichkeit kümmern, in aggressiven Umgebungen zu arbeiten.
Bewertung der besten Ultraschallprüfgeräte für 2025
Budgetsegment
3. Platz: "TUD-1 Sonel Ultraschall-Leck- und Elektroentladungsdetektor"
Das Modell kann den Ort der Druckentlastung (Ort des Austretens von Gasen/Flüssigkeiten, Ort des Vakuumverlusts) genau bestimmen.Es wird verwendet für: Kontrolle der Sauerstoffversorgung, automatische Feuerlöschsysteme, bei der Installation von Klimaanlagen und Lüftungen, Überprüfung von Isolatoren in Kontaktnetzen, Diagnose von Entwicklungsobjekten, Lagerung und Verarbeitung von Erdölprodukten / Gasprodukten, Suche nach Punkten von Schäden an Bremssystemen an Autos, Erkennung elektrischer Entladungen in Niederspannungs-ASUs in einer Entfernung von bis zu 10 Metern und in Hochspannung - in einer Entfernung von bis zu 30 Metern. Es arbeitet nach dem Prinzip, das Auftreten von Materialfehlern zu registrieren, die mit einer starken Änderung der Schallstrahlung, auch im Ultraschallbereich, einhergehen. Das Gerät wandelt die Strahlung in Signale in Ton- / Grafikform um, und der Bediener behebt die Mängel und entscheidet über die Notwendigkeit von Reparaturarbeiten. Das Modell arbeitet berührungslos und muss den Probanden nicht von der Stromversorgung trennen oder die Ausrüstung stoppen. Das Gerät verfügt über eine manuelle Einstellung der Signalstärke, wodurch das Gerät an die individuellen Eigenschaften des Bedieners angepasst werden kann. Die Anwendung ist auch bei Minustemperaturen bis -20 °C möglich. Die empfohlenen Kosten für Einzelhandelsketten betragen 32.760 Rubel
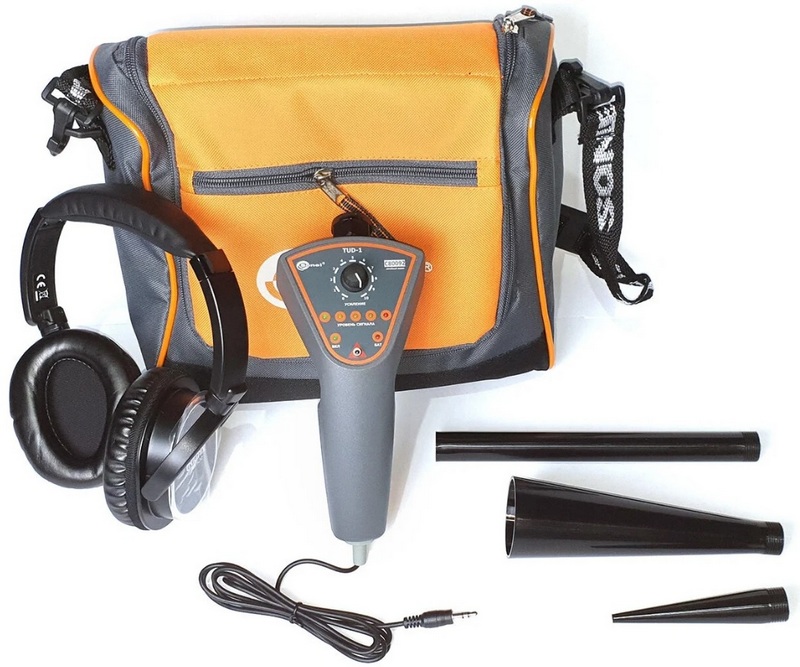
Fehlerdetektor TUD-1 Ultraschall-Leck- und Entladungsdetektor Sonel
Vorteile:
- Praktische Vielseitigkeit;
- Ausreichende Betriebstemperaturen;
- Angemessener Preis.
Mängel:
2. Platz: „Inatest-Härteprüfgerät kombiniert: Ultraschall und dynamisch (Ultraschall-Inatest-U mit Sonde Typ „A“ mit Eichung)“
Dieses Modell gilt als universell, da es möglich ist, viele zusätzliche Geräte zu bestellen, die seine Funktionalität erweitern. Beispielsweise kann es mit 7 verschiedenen Arten von Sensoren für Gusseisen, Stahlzahnräder und -schlitze, dünne Metallprodukte usw. arbeiten.Es ist möglich, unter bestimmten Bedingungen der Härtekontrolle zu arbeiten. Standardmäßig werden drei Varianten von Sensoren zur Messung galvanischer Schwingungen geliefert. Die empfohlenen Kosten für Einzelhandelsketten betragen 71.880 Rubel.
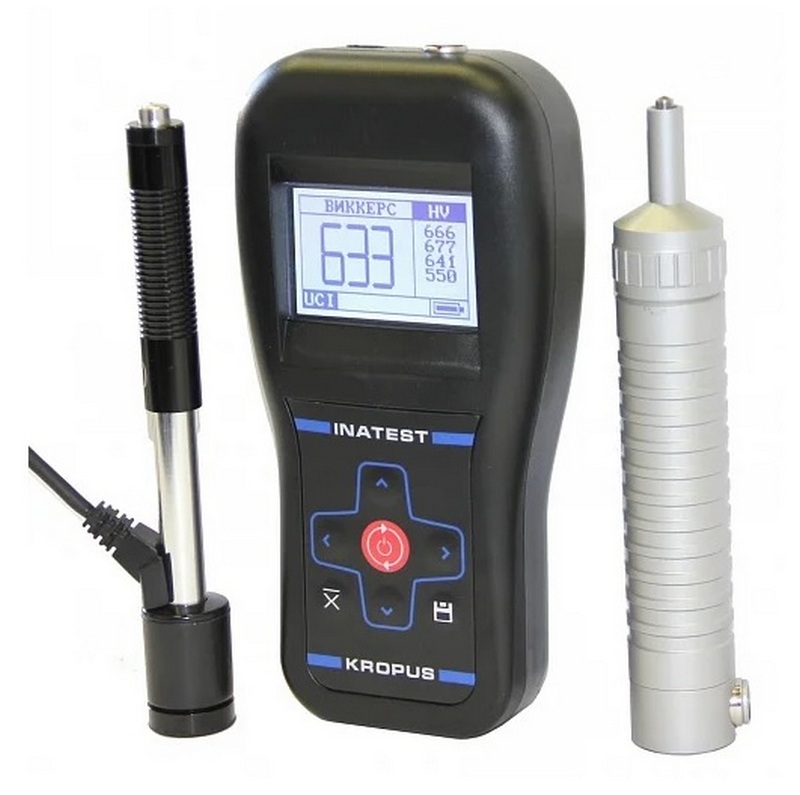
Prüfgerät Inatest Kombi-Härteprüfgerät: Ultraschall und dynamisch (Ultraschall Inatest-U mit Sensor Typ „A“ mit Eichung)
Vorteile:
- Möglichkeit des optionalen Hinzufügens von Sensoren;
- Vielseitigkeit;
- Arbeiten unter besonderen Bedingungen.
Mängel:
- Die Notwendigkeit, zusätzliche Komponenten für eine bestimmte Aufgabe zu kaufen.
1. Platz: "TVM-UD-Härteprüfgerät kombiniert: Ultraschall und dynamisch (Ultraschall-TVM-UD mit Eichung)"
Ein weiteres vorgefertigtes Modell, dessen Qualität durch die Aufnahme in das offizielle Register der von der staatlichen Gesellschaft Russian Railways verwendeten Messgeräte bestätigt wird. Die Modifikation gilt als universell, hat aber standardmäßig nur einen Sensortyp (US). Es können bis zu 10 weitere Sensortypen, bis hin zu dynamischen und galvanischen, angeschlossen werden. Die empfohlenen Kosten für Einzelhandelsketten betragen 85.511 Rubel.
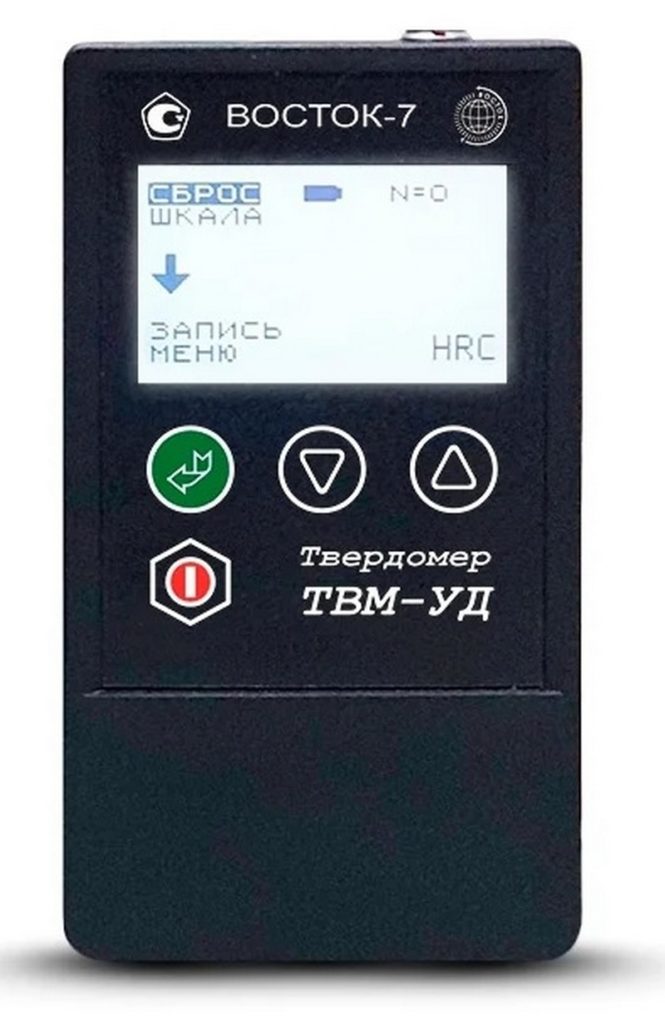
Prüfgerät TVM-UD Kombi-Härteprüfgerät: Ultraschall und dynamisch (Ultraschall-TVM-UD mit Eichung)
Vorteile:
- Fähigkeit, mit 10 verschiedenen Sensoren zu arbeiten;
- Hat Anerkennung auf staatlicher Ebene;
- Kombinierte Arbeitsweise.
Mängel:
Mittleres Preissegment
3. Platz: „UKS-MG4S zur Kontrolle der Festigkeit von Baustoffen und Gesteinen (UKS-MG4 mit Nachweis)“
Dieses fortschrittliche Modell verwendet in seiner Grundkonfiguration nur das Oberflächenwellen-Pumpverfahren, um die Festigkeit von Beton und Stahlbetonprodukten, Ziegeln und Silikatsteinen zu bestimmen.Es hat ein Monoblock-Design, das eine elektronische Einheit mit Konvertern in einem einzigen Gehäuse ist. Zeichnet sich durch eine hohe Genauigkeit aus. Die empfohlenen Kosten für Einzelhandelsketten betragen 92.000 Rubel.
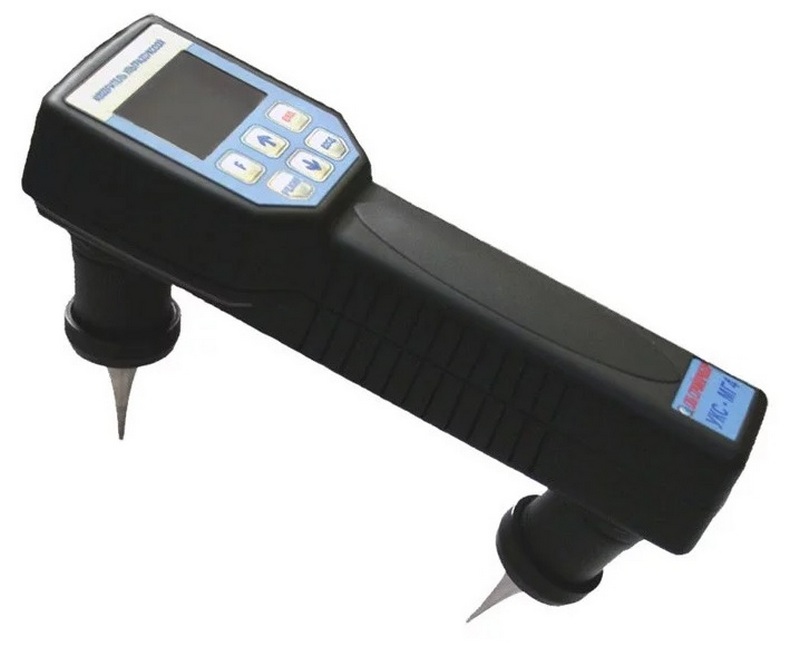
Prüfgerät UKS-MG4S zur Festigkeitsprüfung von Baustoffen und Gesteinen (UKS-MG4 mit Eichung)
Vorteile:
- Enge Spezialisierung (Bau);
- Ausführung in Form eines Monoblocks;
- Ausreichende Genauigkeit.
Mängel:
2. Platz: „PULSAR-2M TFT (geprüft)“
Das ausgezeichnete Gerät, das sich mit der hohen Genauigkeit der durchgeführten Analyse auszeichnet. Es hat ein Design in Form eines Monoblocks und ist perfekt für diensthabende Abteilungen für zerstörungsfreie Prüfungen. Es ist bequem, es sogar in der Tasche zu tragen, da es kleine Abmessungen hat. Das Display ist farbig und alle Bedienelemente sind intuitiv. Es gibt einen Speicherblock zum Speichern einer großen Menge von Ergebnissen. Die empfohlenen Kosten für Einzelhandelsketten betragen 138.000 Rubel.
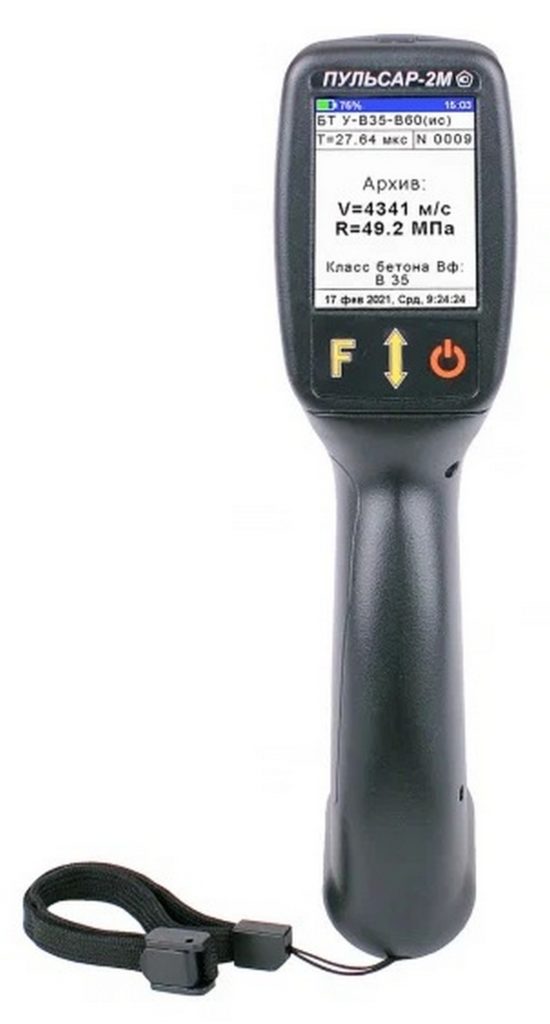
Fehlerprüfgerät PULSAR-2M TFT (mit Eichung)
Vorteile:
- Hohe Funktionalität entspricht dem angegebenen Preis;
- Maximale Portabilität;
- Farbbildschirm.
Mängel:
1. Platz: „PULSAR-2.1 (geprüft)“
Sehr teure und multifunktionale Probe. Es kann in einer Vielzahl von Anwendungen eingesetzt werden, von der Konstruktion, wo Ergebnisse mittlerer Genauigkeit erforderlich sind, bis hin zur Hochpräzisionstechnik, wo Analysen bis in den Mikrometerbereich benötigt werden. Das Kit wird mit allen möglichen Arten von Sensoren geliefert. Die empfohlenen Kosten für Einzelhandelsketten betragen 140.000 Rubel.
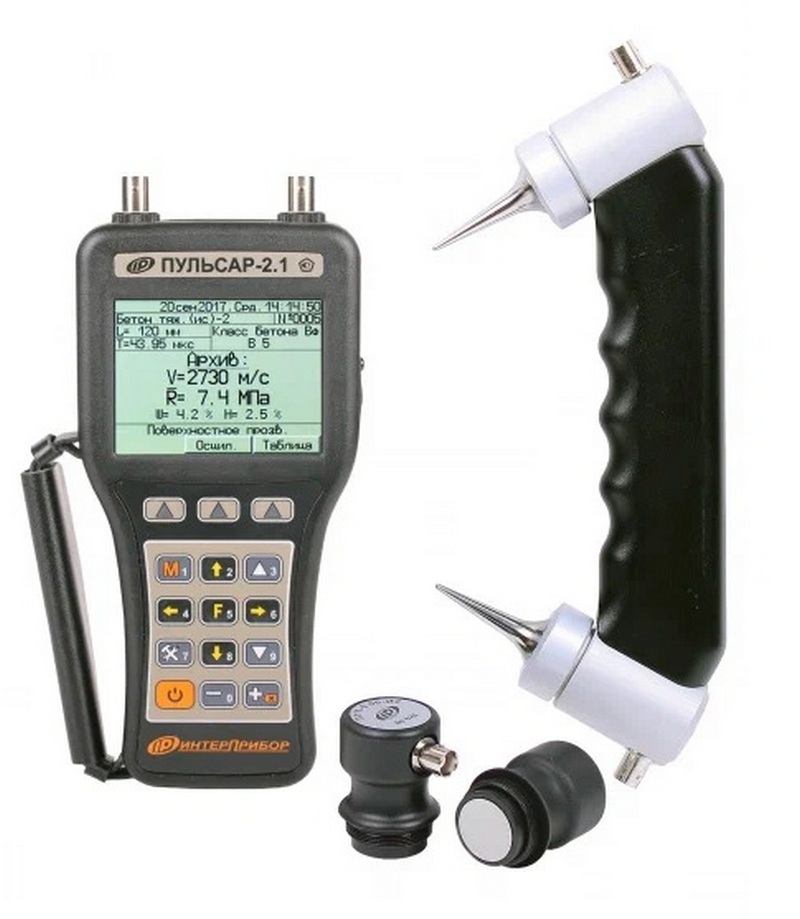
Fehlerprüfgerät PULSAR-2.1 (mit Eichung)
Vorteile:
- Ausreichendes Verhältnis von Ausstattung und Preis;
- Breites Anwendungsspektrum;
- Verbesserte Genauigkeit.
Mängel:
Premiumklasse
2. Platz: "Tauchstrahler SG-18 28kHz 900W mit Generator"
Dieses Gerät dient zur Diagnose von Rohrleitungen mit beliebigem Durchmesser, ist ein hochpräzises stationäres Gerät und wird zur Qualitätskontrolle von Walzgut in Werkstätten eingesetzt. Seine Sonden kommen besonders gut mit Rohren mit unregelmäßiger Geometrie und mit abnehmendem / zunehmendem Durchmesser über die gesamte Länge der Leitung zurecht. Das Kit beinhaltet: Plattform, Generator, Hochfrequenzsonde, Aufbewahrungskoffer. Die empfohlenen Kosten für Einzelhandelsketten betragen 170.000 Rubel.
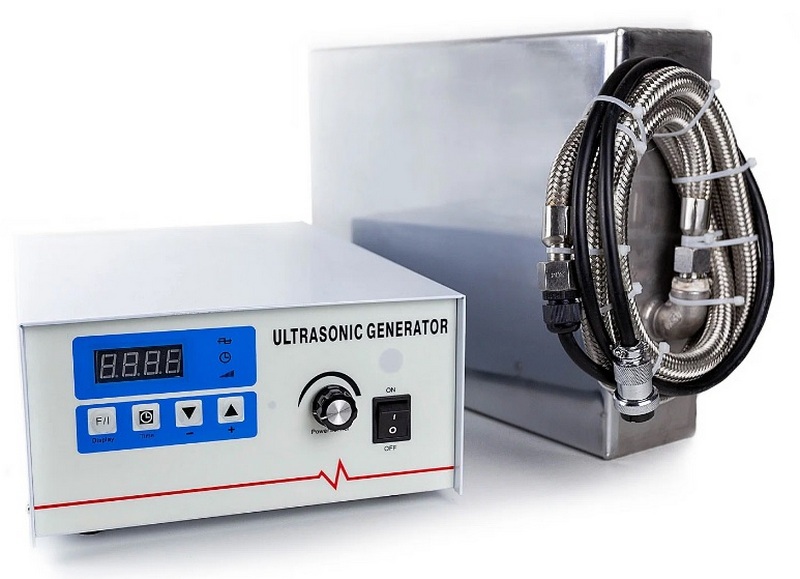
Fehlersuchgerät Tauchstrahler SG-18 28kHz 900W mit Generator
Vorteile:
- Erhöhte Genauigkeit;
- Stationäre Platzierung;
- Fähigkeit, mit nicht standardmäßigen Objekten zu arbeiten;
- Ein Jahr Garantie.
Mängel:
- Begrenzter (nur industrieller) Anwendungsbereich.
1. Platz: "Ultraschallgerät PULSAR-2.2 (mit Verifizierung)"
Die neueste und modernste Modifikation der beliebten russischen Gerätemarke. Die finale Release-Software ist darauf installiert, es ist nun möglich, Testgraphen in Dynamik anzuzeigen. Das Kit enthält alle gängigen Sensoren, das Gerät hat kleine Abmessungen. Die empfohlenen Kosten für Einzelhandelsketten betragen 222.000 Rubel.
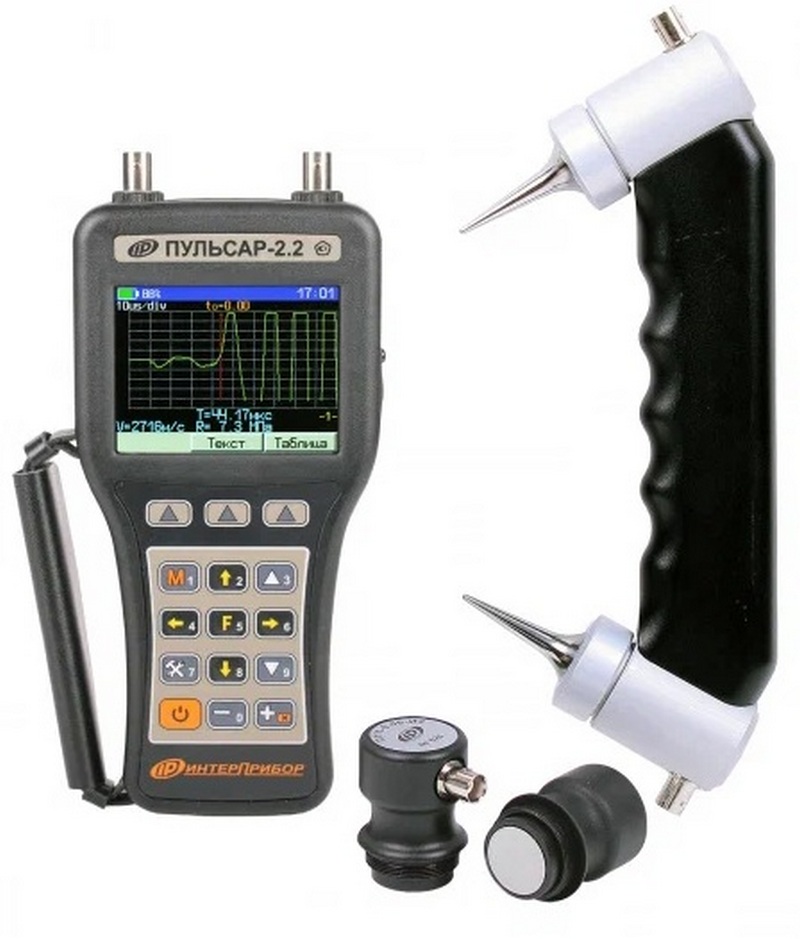
Fehlersuchgerät Ultraschallgerät PULSAR-2.2 (mit Eichung)
Vorteile:
- Neueste Softwareversion;
- Gute Ausstattung;
- Kleine Größen.
Mängel:
Fazit
Es ist immer daran zu erinnern, dass die betreffenden Hochpräzisionsgeräte in Bezug auf Gewicht, Abmessungen, Art der Stromversorgung, Methoden zur Fehlererkennung und Vibrationsfestigkeit den Anforderungen der staatlichen Norm Nr. 23049 von 1984 entsprechen müssen.Darüber hinaus muss jedes Modell über ein bestimmtes Minimum an Arbeitsblöcken verfügen, mit denen Sie die meisten Standardoperationen ausführen können.